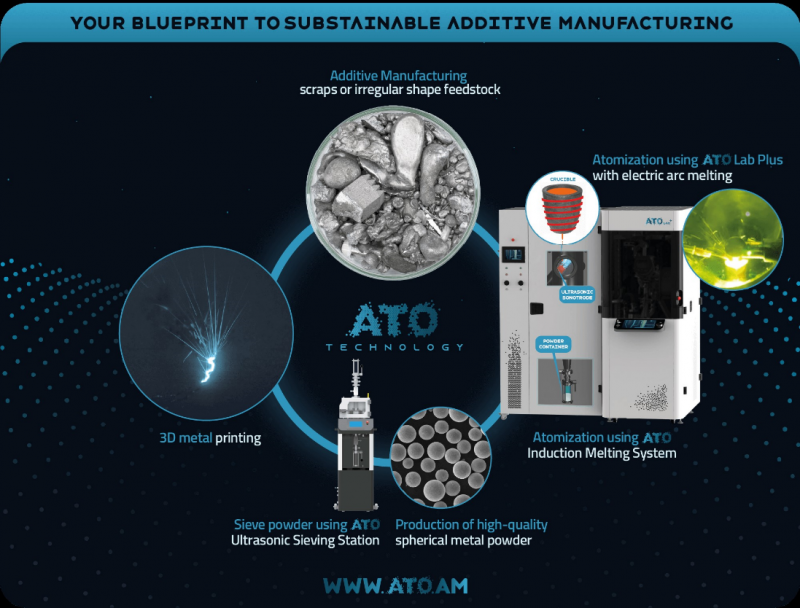
3D Lab sp zoo, based in Warsaw, Poland, has revolutionized metal powder production with its innovative ATO Induction Melting System (IMS). This system enhances the company’s ultrasonic metal atomisers, enabling the design and manufacture of metal powders in a streamlined, single-step process. The advancement significantly impacts alloying, material processing, and sustainable manufacturing.
Key Features of the ATO Induction Melting System
The ATO IMS melts materials at temperatures up to 1700°C. This high-temperature capability enables advanced material processing and is especially effective for atomising metals with low melting points, such as copper and aluminium. By adding the IMS module to the ATO ultrasonic atomisers, 3D Labs prevents element evaporation during atomisation, stabilising the chemical composition of alloys.
Two Operational Modes: Crucible and Rod
The IMS offers two distinct operational modes: crucible and rod.
-
Crucible Mode: This mode melts and atomises feedstock in various forms, including chips, powders, pellets, and irregularly shaped materials. It suits material recycling and sustainable manufacturing. The crucible configuration has an open hole, preventing contamination from plugs during the process. The material then moves from the crucible onto the atomisation platform through the pressure difference.
-
Rod Mode: The rod configuration minimises contamination by eliminating contact with the crucible. This mode ensures high-purity powder production, ideal for demanding applications like those in the medical industry, where purity is crucial.
Alloying and Single-Step Process for Advanced Materials
IMS not only processes conventional materials but also enables alloy development through a single-step process combining preparation, melting, and atomisation. This technology results in powders with perfect sphericity and controlled particle size distribution (PSD), making it ideal for various Additive Manufacturing technologies.
A notable example is the development of a high-entropy aluminium alloy using IMS technology. The process included loading pure aluminium, iron, chromium, and niobium into the system. The system melted and homogenised these materials with stirring and argon gas. The molten metal then moved to the atomisation platform using a pressure differential, where ultrasonic atomisation converted it into fine powder.
Perfecting High-Entropy Alloys for Additive Manufacturing
The resulting high-entropy aluminium alloy powder exhibited an exact chemical composition, perfect sphericity, and a narrow particle size distribution. SEM-EDS analysis confirmed the powder’s suitability for Additive Manufacturing and advanced metallurgy applications.
Conclusion
The ATO Induction Melting System (IMS) from 3D Labs brings significant advancements to alloying and metal powder production. By streamlining the process into a single-step operation, the IMS produces high-quality, spherically shaped powders with controlled particle size distribution. This innovation has great potential across industries, including Additive Manufacturing and advanced metallurgy technologies.
Leave a Reply
You must be logged in to post a comment.