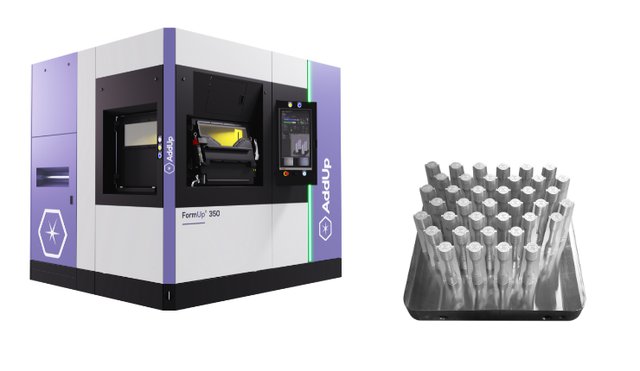
AddUp Excels in High-Cycle Fatigue Study on IN-718 for Aerospace
AddUp, a leading additive manufacturing company based in Cébazat, France, has outperformed competitors in a high-cycle fatigue (HCF) study by the United States Air Force (USAF). The study, part of the Small Business Innovation Research (SBIR) program, aimed to develop manufacturing and heat treatment guidelines for Inconel 718 (IN-718) components. IN-718 is critical in aerospace and defense applications, where high fatigue resistance is crucial for long-term reliability.
Study Focus: Optimizing IN-718 for Aerospace Use
The study, led by REM Surface Engineering, examined how heat treatment and printing parameters affect the mechanical properties of additively manufactured IN-718. Key tests included Hot Isostatic Pressing (HIP) versus non-HIP treatments, contour versus non-contour melting, and different build angles (0°, 45°, and 90°). The goal was to enhance IN-718’s tensile strength and fatigue life for aerospace applications.
AddUp’s Performance with Advanced Manufacturing Technology
AddUp was named the top vendor (V1) in the study. Its FormUp 350 system, paired with REM Surface Engineering’s Extreme ISF Process, achieved superior material properties. This combination significantly enhanced fatigue strength, which is a critical factor for aerospace applications. Furthermore, the FormUp 350 employs fine powder and roller recoater systems to achieve high-quality finishes. In addition, REM’s surface finishing technology further improved both fatigue and corrosion resistance, boosting the overall performance of the components.
Importance of Fatigue Resistance in Aerospace and Defense
The study highlights the importance of fatigue resistance in aerospace and defense. Component reliability is essential for mission success. Additive manufacturing and surface finishing technologies improve the fatigue life of IN-718 components. These advancements reduce maintenance costs, extend component lifespans, and minimize downtime in high-stress aerospace environments.
Implications for Future Aerospace Applications
Dr. Augustin Diaz, Advanced Manufacturing and Innovation Manager at REM Surface Engineering, noted the importance of these findings. The research not only benefits the Department of Defense (DoD) but also provides insights into advancing additive manufacturing in aerospace. The successful integration of AddUp’s PBF-LB technology with REM’s surface finishing process is expected to impact future aerospace component production.
Leave a Reply
You must be logged in to post a comment.