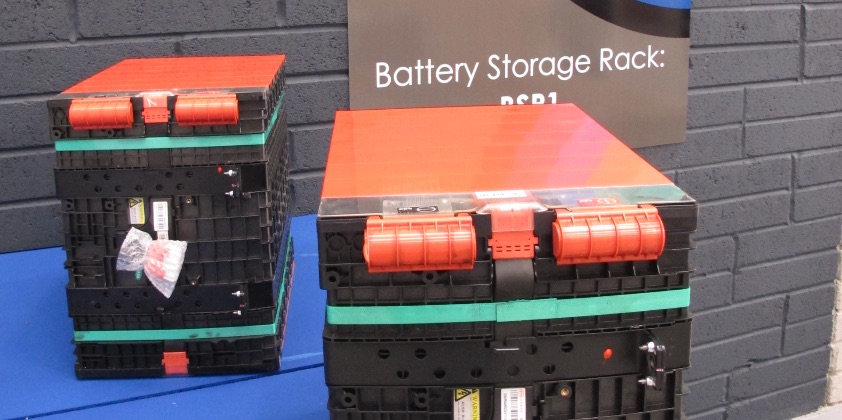
Pioneering Eco-Friendly Solutions for Sustainable Battery Production
Altilium, a lithium-ion battery recycler based in the U.K., has announced the launch of lithium iron phosphate (LFP) battery recycling. This move is a significant step forward in supporting global electric vehicle (EV) and energy storage systems (ESS) manufacturers. Altilium’s commitment to LFP battery recycling solutions highlights its dedication to reducing the environmental impact of battery production in the region.
Altilium’s proprietary EcoCathode technology is central to this initiative. It boasts a high recovery rate of more than 97 percent of lithium and 99 percent of graphite from end-of-life LFP batteries. The company aims to enable automotive original equipment manufacturers (OEMs) to meet regulatory targets and sustainability goals. Additionally, this ensures valuable resources are reused in the production of new batteries. This makes LFP battery recycling solutions critical for the future.
LFP Battery Recycling: Challenges and Opportunities
While nickel cobalt manganese (NMC) batteries dominate the EV market, the rise of LFP batteries presents new opportunities for recycling. LFP batteries are expected to grow from 18 percent of the U.K. EV market in 2027 to 25 percent by 2035. This is according to the Advanced Propulsion Centre. However, recycling LFP batteries is challenging because iron and phosphate have less value than the nickel and cobalt found in NMC batteries.
Altilium addresses these challenges by focusing on high-value material lithium. The company also recovers graphite for reuse in new anode production. This innovative approach ensures the commercial viability of LFP battery recycling solutions. Additionally, it helps to establish a circular battery economy in the U.K.
Christian Marston, Altilium’s Chief Operating Officer, commented on the company’s role in the transition, saying, “We are pioneering solutions to ensure LFP batteries are not only recovered, but play a key role in a U.K. circular battery economy. Our EcoCathode technology makes LFP recycling environmentally essential and commercially viable.” Effective LFP battery recycling solutions like these are crucial for sustainability.
Expanding Capabilities in Battery Recycling
Altilium’s operations also extend to the recycling of NMC batteries from two U.K.-based automotive OEMs, as well as gigafactory production scrap, at its ACT1 and ACT2 facilities. The recently opened ACT2 plant in Plymouth, England, recycles 300 kilograms of black mass per day, recovering lithium and other battery metals. The company’s upcoming Teesside hub is set to become one of Europe’s largest EV battery recycling facilities. It will have the capacity to process scrap from over 150,000 EVs annually. The facility is designed to handle a mix of battery chemistries, including LFP. This further strengthens the U.K.’s battery supply chain and its sustainable transport goals. This highlights the importance of diverse LFP battery recycling solutions.
Leave a Reply
You must be logged in to post a comment.