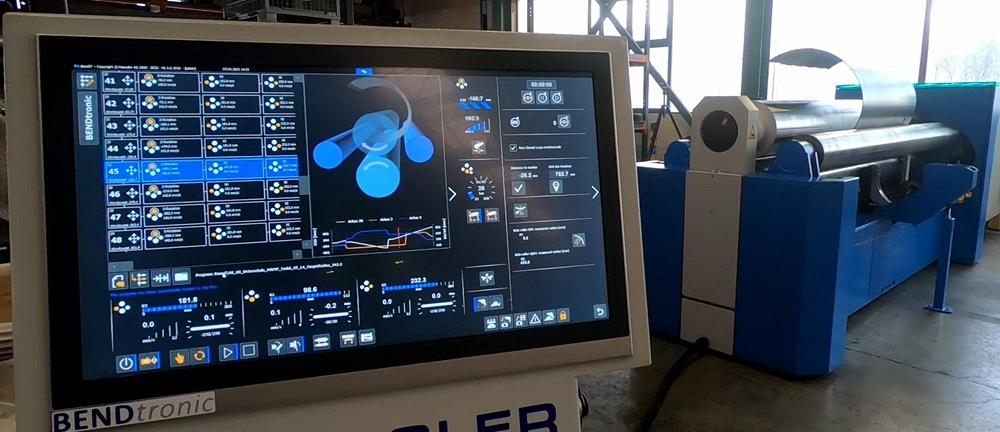
Advance Products & Systems (APS) has upgraded its manufacturing capabilities with the addition of the EVO four-roll plate rolling machine. This new equipment replaces outdated manual machinery and addresses long-standing production bottlenecks. The upgrade improves efficiency, precision, and production speed, key concerns for the company.
Streamlining Production with Automated Plate Rolling Technology
Before the upgrade, APS struggled with an old machine that required manual adjustments and was slow to produce the company’s wall sleeves. The outdated equipment made it difficult to maintain tight tolerances of 1/16 inch for pipeline applications. The new EVO machine automates the plate rolling process, offering real-time adjustments and enhanced precision. Built-in cameras and a measuring arm ensure each part meets specifications, increasing product consistency.
Improved Precision, Efficiency, and Shorter Lead Times
The new EVO system allows APS to produce parts with greater precision than before. Previously, maintaining tight tolerances was a challenge, but with this automated machine, APS can now meet strict quality standards consistently. Additionally, the automation has significantly reduced lead times. What once took four to six weeks to produce can now be completed in two to three weeks, offering quicker turnarounds for customers.
Automation Transforms APS’s Shop Floor
Since the installation of the EVO machine, APS has experienced improved production flow and operational efficiency. The automation minimizes human error and reduces the need for manual intervention, leading to higher-quality products. APS’s automation team ensured smooth integration of the new technology, marking a milestone in the company’s journey toward fully automating its operations.
Preparing for the Future of Manufacturing
APS’s transition to an automated plate rolling system reflects the broader trend in the manufacturing industry toward automation. As the company continues to explore new technologies, the EVO machine helps them stay competitive in the market. By embracing automation, APS enhances both its manufacturing process and customer satisfaction.
Leave a Reply
You must be logged in to post a comment.