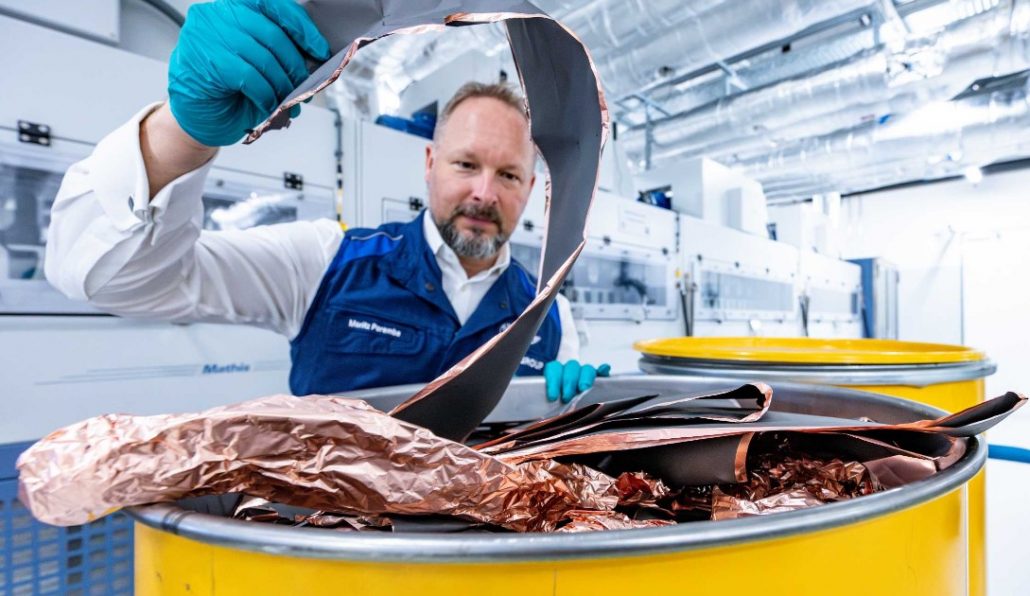
BMW Group is advancing its sustainability efforts with an innovative approach to battery material recycling. The company has opened a Cell Recycling Competence Centre (CRCC) in Kirchroth, Bavaria, to implement a “direct recycling” process. This method reduces production costs and enhances battery material efficiency. It involves dismantling residual materials from battery cells and reusing valuable components such as lithium, cobalt, graphite, manganese, nickel, and copper. Unlike traditional recycling methods, which rely on energy-intensive chemical or thermal treatments, direct recycling reintegrates these materials seamlessly into the production cycle.
Investment and Infrastructure for Circular Battery Production
BMW is investing €10 million in the CRCC, located within the Kirchroth-Nord industrial park. The facility will focus on energy efficiency, utilizing energy recovered from discharged battery cells. It will also rely on solar power generated by photovoltaic panels on the roof. This innovative setup allows BMW to scale its recycling operations to handle significant amounts of battery material annually. By reducing waste and maximizing material reuse, BMW strengthens its commitment to sustainable manufacturing.
Collaborative Approach to Achieving Circular Economy Goals
BMW is partnering with Encory GmbH, a joint venture with Interzero Group, to manage the CRCC. Encory specializes in logistics, recycling, and remanufacturing of vehicle components, ensuring efficient recycling processes. BMW’s in-house Battery Cell Competence Centres (BCCCs) will work closely with the CRCC to integrate recycled materials into production. This collaboration fosters a closed-loop system for battery materials, reinforcing BMW’s sustainability goals.
Supporting Circular Economy and Sustainable Manufacturing
BMW’s circular economy initiative aims to reduce reliance on newly mined raw materials and lower environmental impact. By reusing materials like lithium and cobalt in battery production, BMW advances both environmental sustainability and economic efficiency. This initiative aligns with BMW’s principles of rethink, reduce, reuse, and recycle. These principles are applied throughout all stages of vehicle production, from design to end-of-life vehicle recycling.
Leave a Reply
You must be logged in to post a comment.