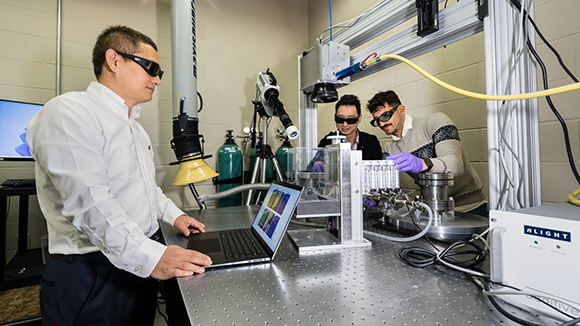
Researchers at the University of Wisconsin-Madison (UW-Madison) have found an innovative way to reduce common defects in metal parts made using Laser Beam Powder Bed Fusion (PBF-LB) additive manufacturing. Their new approach uses a ring-shaped laser beam. This technology helps address defects like pores, rough surfaces, and large spatters, which can harm the quality of parts. The research, published in International Journal of Machine Tools and Manufacture, marks a significant improvement in the production of metal parts.
Revolutionizing Metal Additive Manufacturing
Traditional research usually tackles one type of defect at a time. However, UW-Madison’s method uses a ring-shaped laser beam, which can address multiple defects at once. This change improves the quality of parts and speeds up production. According to Associate Professor Lianyi Chen, this new technology can benefit industries such as aerospace, medical devices, and energy, which need high-performance parts.
Addressing Common Defects with Ring-Shaped Lasers
Metal parts made through additive manufacturing often suffer from defects such as pores, voids, and rough surfaces. These issues weaken the parts and make them unreliable. The research from UW-Madison addresses these issues and improves the quality of parts made through PBF-LB. With this breakthrough, manufacturers can produce stronger and more reliable parts.
Advanced Imaging for Deeper Insights
To understand the manufacturing process better, the team used synchrotron X-ray imaging at the Advanced Photon Source, Argonne National Laboratory. This imaging method allowed them to observe the material’s behavior during production. By combining real-time X-ray imaging with simulations, the team identified key factors that reduce instability. These findings allow the production of thicker layers without causing instability, improving productivity.
A Collaborative Effort for the Future of Manufacturing
This research was a collaboration between UW-Madison and Argonne National Laboratory. Key contributors included PhD student Jiandong Yuan and collaborators Qilin Guo, Luis Escano, and others. The study was funded by the National Science Foundation and the Wisconsin Alumni Research Foundation. The use of a ring-shaped laser beam enhances the quality and productivity of metal additive manufacturing. This innovation promises a more efficient and reliable production process, especially for high-performance parts.
Leave a Reply
You must be logged in to post a comment.