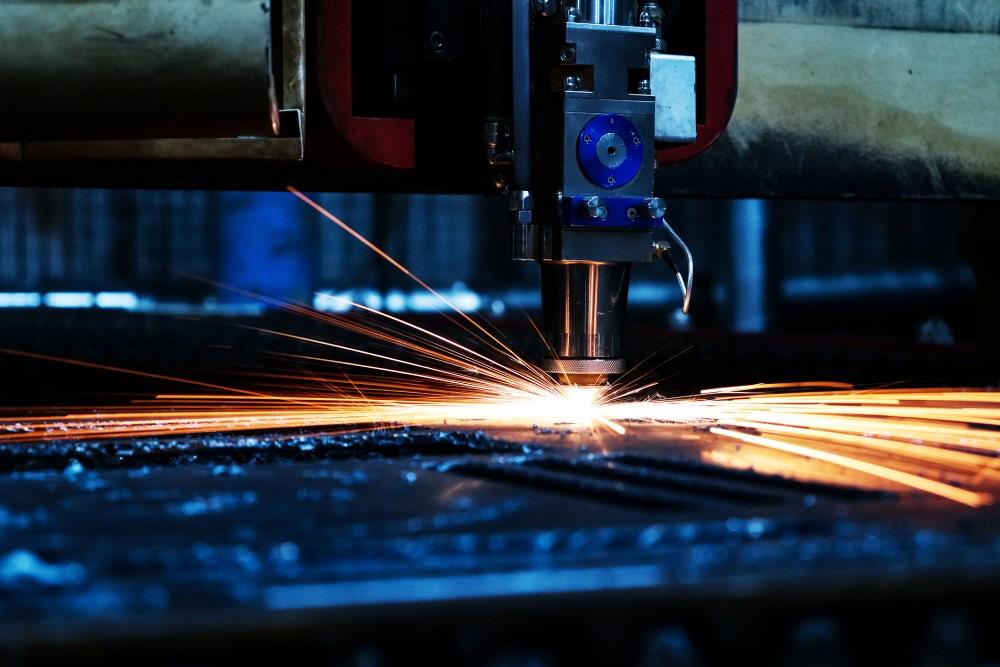
Productivity Demands a Strategic Approach
Phil Picardat, automation product manager at AMADA AMERICA, emphasized the importance of strategic planning and commitment to excellence for improving productivity in metal fabrication. Quoting Paul Meyer, he underscored that productivity is the outcome of thoughtful effort, rather than just hard work. This perspective is crucial, especially in the context of high-product-mix environments where metal fabricators manage multiple jobs simultaneously.
Addressing Systemic Challenges
Picardat outlined three critical strategies for sustainable productivity: reviewing workflow, enhancing communication, and monitoring utilization. These elements are vital for overcoming systemic challenges and optimizing the benefits of advanced fabrication technologies. He noted that in today’s labor market, simply adding machines and personnel is no longer a viable solution due to skilled labor shortages exacerbated by the COVID-19 pandemic.
Understanding Workflow
To break the cycle of inefficiency, fabricators must first analyze their workflows. Picardat advised starting with lean manufacturing principles, such as maintaining clear work instructions and organized workspaces. He pointed out that small changes in one area can significantly impact overall productivity. For example, consistent part presentation to operators is essential; otherwise, errors can occur, leading to costly mistakes down the line.
The Role of Design for Manufacturability (DFM)
Improving communication within the fabrication team is crucial, particularly concerning design changes. Picardat highlighted the impact of DFM, stating that design decisions can affect labor, material costs, and overall process efficiency. He cited a case where redesigning a 16-part assembly into a four-part subassembly drastically reduced lead times, demonstrating the power of collaborative communication across departments.
Utilizing Data for Optimization
Monitoring utilization is another cornerstone of improving productivity. Picardat introduced the Industrial Internet of Things (IIoT) as a tool for gathering data on machine performance and identifying bottlenecks. This data-driven approach allows fabricators to pinpoint inefficiencies that may go unnoticed during direct observation.
Maximizing Technology Investments
With comprehensive insights into workflow, communication, and utilization, fabricators can fully leverage new technologies. Picardat illustrated how automation technologies—like real-time laser monitoring and advanced part sorting—can streamline operations. He emphasized that effective automation is not solely about speed; it’s about integrating processes for optimal system performance.
Embracing Future Innovations
As the industry looks ahead, the integration of autonomous mobile robots (AMRs) will play a significant role in enhancing operational efficiency.
Picardat envisions a future where tracking part flow with AMRs will provide invaluable data to optimize production processes across the entire value stream.
In conclusion, metal fabrication productivity hinges on a holistic approach that combines workflow analysis, effective communication, and data utilization, setting the stage for the next generation of operational excellence.
Leave a Reply
You must be logged in to post a comment.