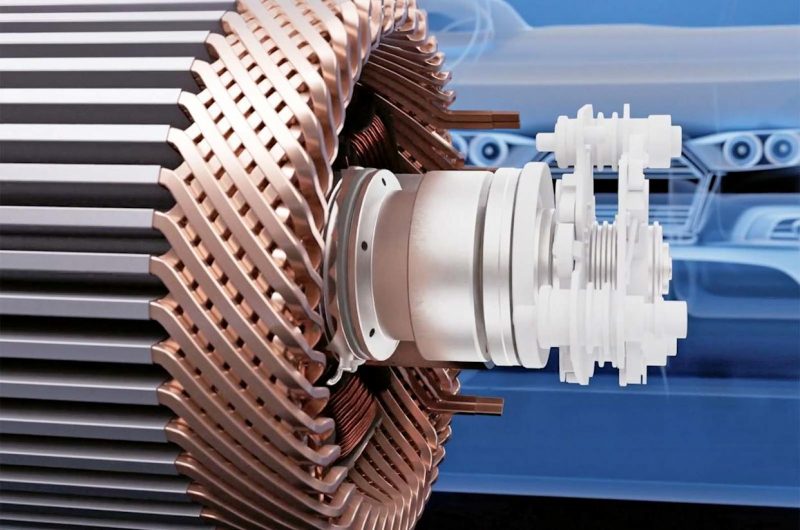
A European initiative is reducing dependence on virgin rare earth elements (REEs) in electric vehicle motors.
The “Sustainable Recovery, Reprocessing, and Reuse of Rare-Earth Magnets in a Circular Economy” project launched in 2019.
It focuses on improving motor recyclability and finding new material solutions for permanent magnet motors.
Recycling Process Offers Lower Energy Use
Magnets in motors are hard to remove cleanly and often break into powder that sticks to ferrous scrap.
However, hydrogen processing of magnet scrap (HPMS), developed at Birmingham University, changes that.
The process creates a non-magnetic powder without detaching the magnets from the rotor.
As a result, the powder can be reused to make new magnets.
This method uses only 12% of the energy needed to produce magnets from virgin REEs.
ZF Friedrichshafen has tested motors using HPMS and found their performance nearly equal to those using mined REEs.
New Motor Designs Reduce REE Demand
In addition to recycling, the project also supports motors that do not need permanent magnets.
Externally excited synchronous motors, used by Renault since 2012, use electromagnetic windings instead of REE-based magnets.
However, they require brushes to transfer current, which introduces friction and wear.
ZF’s I2SM (in-rotor inductive excited synchronous motor) solves this problem.
It places a small inductive generator inside the rotor shaft to excite the motor without using brushes.
Therefore, the I2SM combines high efficiency with reduced maintenance.
Conclusion: Toward a Sustainable EV Future
This project shows that Europe can cut REE demand in two key ways.
First, it recycles magnets using low-energy processes like HPMS.
Second, it promotes motor designs that avoid rare earth magnets entirely.
Together, these efforts support a greener, circular economy in the electric vehicle industry.
SuperMetalPrice will continue tracking REE innovation and EV supply chain trends.
Leave a Reply
You must be logged in to post a comment.