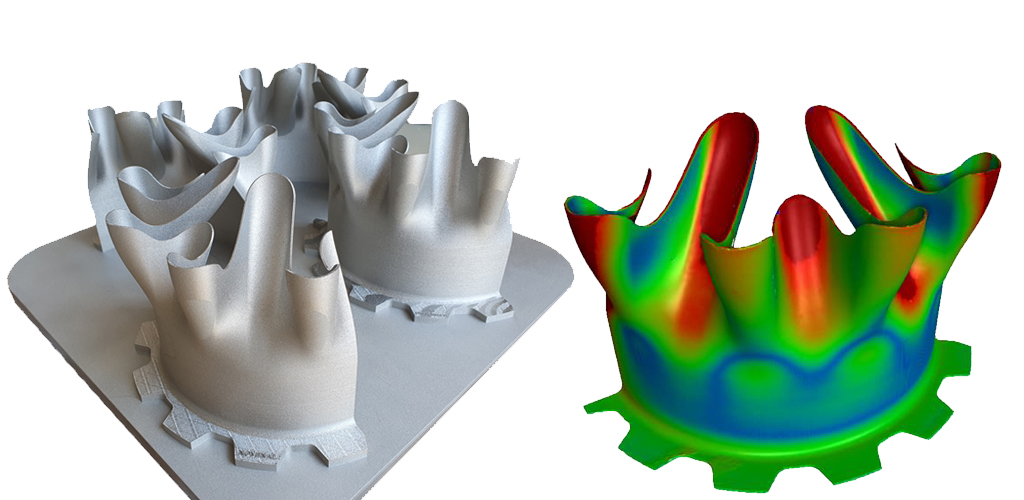
Hexagon’s Manufacturing Intelligence division has introduced a game-changing solution aimed at improving the precision of metal 3D printing. This Advanced Compensation approach combines process simulation and 3D scan compensation to eliminate the trial-and-error that typically plagues the manufacturing of precision metal parts using laser powder bed fusion (LPBF) technology. This new method helps reduce distortions and achieve high-quality, accurate results in the production of large, complex metal components, offering a more streamlined, cost-effective approach to additive manufacturing.
Addressing Industry Challenges with High-Precision Manufacturing
Industries such as aerospace, medical prosthetics, and machine building demand high-precision, repeatability, and dimensional accuracy. However, LPBF, though efficient for metal 3D printing, often faces challenges like deviations, defects, and inconsistencies, especially in applications where reliability is crucial. To address these issues, Hexagon’s new system combines advanced simulation tools with metrology-based compensation. As a result, it enhances the quality of metal prints and minimizes errors, even in the most complex geometries. This solution is particularly beneficial for high-value applications that require exact tolerances.
Efficiency Gains with Reduced Trials and Material Waste
One of the standout features of Hexagon’s Advanced Compensation is its ability to achieve exceptional precision with less material waste and fewer print trials. This solution ensures that surface profiles meet 98%-100% tolerance, even for parts with thin walls prone to buckling or challenging materials. In tests, the system has enabled 0.2mm precision in stainless-steel parts after just one prototype build. This means that companies can reduce time, material waste, and support structure requirements in the production of metal parts, making it more efficient than traditional methods.
Simulation and Scanning Tools Enable Faster, More Accurate Printing
The heart of Hexagon’s solution lies in its integration of Simufact Additive software and VGSTUDIO MAX scanning tools. Simufact Additive simulates distortions and shrinkages before printing begins, reducing the number of trials needed to perfect a part. VGSTUDIO MAX compensates for local distortions by adjusting the printable mesh. It uses optical or computed tomography (CT) scans to create highly accurate parts. The system is designed to be accessible, requiring no prior metrology expertise. This makes it easier for manufacturers to achieve high-precision results with minimal effort.
Scaling Up Efficiency with a Data-Driven Approach
Hexagon’s data-driven system not only ensures precision but also improves efficiency in large-scale additive manufacturing applications. The system uses digital twin technology, considering machine parameters and material behavior. It helps companies refine processes for both small batch production and large-volume manufacturing. This scalable approach gives manufacturers flexibility to handle complex projects. It also ensures ‘second-time-right’ prints, saving time, costs, and material.
Leave a Reply
You must be logged in to post a comment.