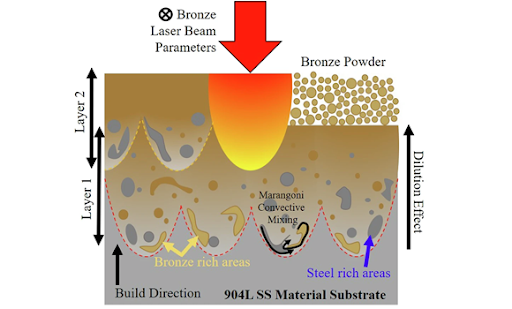
Recent research from Pennsylvania State University, University Park, USA, published in npj Advanced Manufacturing, explores how build orientation impacts the performance and quality of multi-material parts created using Laser Beam Powder Bed Fusion (PBF-LB) Additive Manufacturing. This study provides valuable insights into how build orientation influences material compatibility, process-induced defects, and interfacial formation mechanisms in multi-material applications.
Multi-Material Laser Beam Powder Bed Fusion: A Complex Process
The research investigates multi-material PBF-LB by studying a complex gyroid structure made of 904L stainless steel and bronze. Researchers focused on several critical factors, such as melt pool characteristics, grain morphology, defects, and mechanical properties of the printed materials. Moreover, advanced techniques, including flexural testing with digital image correlation (DIC), finite element analysis (FEA), and intermittent micro-CT, were used to analyze fracture mechanisms in PBF-LB.
Multi-material PBF-LB enables the production of intricate, multifunctional components. However, the knowledge gained from processing single-material components must be adapted to account for the interactions between multiple materials during the build process.
Key Findings from the Study
The researchers made several key observations regarding how build orientation affects multi-material parts. These findings are essential for optimizing the PBF-LB process and improving the overall quality of printed components.
Build Orientation and Material Interfaces
Defects and melt-pool morphology at the interface of additively manufactured parts depend heavily on build orientation. Notably, the build direction plays a critical role in determining the presence and severity of interfacial defects. Therefore, adjusting the build direction is crucial for minimizing these defects.
Insignificant Effect of Part Orientation
Interestingly, part orientation relative to the recoating direction had minimal effect on interfacial defects. This finding suggests that build direction is far more influential than recoating direction in determining the interface’s quality. As a result, manufacturers may want to prioritize optimizing build direction over recoating orientation.
Key Mechanisms of Elemental Diffusion
Rapid solidification, Marangoni convection, and the “dilution” effect were identified as the primary mechanisms driving elemental diffusion at the interface. Understanding these factors is essential for improving material mixing and bonding during the PBF-LB process. In particular, these mechanisms help ensure more uniform material behavior throughout the build.
Cracking and Grain Boundary Solute Segregation
The study observed multi-scale cracking within the 904L stainless steel region near the interfacial plane. This cracking resulted from mismatched thermophysical properties. Furthermore, grain boundary solute segregation in areas with high steel-to-bronze ratios created crack-initiating sites, which, under solidification and thermal strain loading, led to regional solidification cracking.
Improved Bonding with Balanced Material Mixing
The study revealed that regions with a balanced mix of steel and bronze, where the volume fraction of bronze sufficiently backfilled crack-initiating sites, demonstrated improved metallurgical bonding. Consequently, this balanced material mixing resulted in stronger and more reliable interfacial bonds, which are crucial for the structural integrity of multi-material parts.
Premature Failure in Complex Structures
Mechanical testing of complex TPMS (Topological Parametric Material Structures) revealed premature failure from nano- and micron-scale cracking near the interface. Notably, this failure occurred more frequently than predicted by finite element analysis, emphasizing the need to better understand material interactions during the build process. Therefore, future studies should focus on improving prediction models for material behavior.
Conclusion
The research on multi-material Laser Beam Powder Bed Fusion underscores the significant role that build orientation plays in the performance and quality of printed parts. The findings provide valuable insights for improving process control and optimizing material compatibility in multi-material additive manufacturing. Understanding the effects of build orientation, melt pool dynamics, and grain boundary segregation can ultimately lead to better designs, enhanced material properties, and more reliable production of complex components.
Leave a Reply
You must be logged in to post a comment.