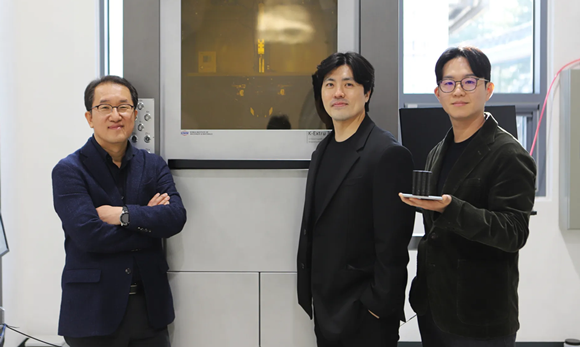
Innovative Manufacturing for Next-Generation Motors
The Korea Institute of Machinery & Materials (KIMM) has pioneered a magnetic Additive Manufacturing (AM) technology to produce high-performance motors without using traditional molds. This breakthrough benefits industries such as robotics, Electric Vehicles (EVs), and mobility solutions, where compact, high-output motors are essential. In addition, the technology allows the creation of complex, lightweight, and efficient motors, offering superior performance compared to traditional methods.
Axial Flux Motors: High Torque and Compact Design
KIMM applied this magnetic AM technology to develop axial flux motors, which are known for their high efficiency in torque-heavy applications and space-constrained environments. For example, KIMM created a 500W-class motor with an output density of over 2.0 kW/L, much higher than conventional motors of similar size. This achievement demonstrates AM’s potential to revolutionize motor performance, especially in areas where compactness and power density are crucial, such as mobility solutions.
Collaborative Research for Technological Advancement
This breakthrough resulted from the collaboration between Dr. Taeho Ha’s team at KIMM, Dr. Taehun Kim’s team from the Korea Institute of Materials Science, and Professor Wonho Kim’s team at Gachon University. They focused on overcoming key challenges in motor design, materials, and process optimization. As a result, they developed a comprehensive solution that enables the production of high-performance motors with better output and efficiency.
Benefits Over Traditional Manufacturing Methods
Traditional motor manufacturing relies heavily on molds, which contribute to material waste and higher costs. However, the new magnetic AM technology eliminates molds, offering greater design freedom and reduced material waste. Consequently, this technology makes the production of high-performance motors more cost-effective and flexible, meeting the growing demand for customizable solutions across various industries.
Future Implications and Expanding Applications
This technology not only improves motor performance but also lays the foundation for future advancements in manufacturing. By producing motors with less waste and greater efficiency, it can drive innovation in electric transportation, robotics, and renewable energy. Furthermore, Dr. Taeho Ha believes this technological leap represents a shift in motor manufacturing, unlocking new possibilities in next-generation industrial fields. KIMM plans to continue advancing this technology by integrating it with 3D printing for high-functional materials.
Support from National Research Initiatives
KIMM’s research was supported by the Basic Research Program for Additive Manufacturing equipment and the Nano & Materials Technology Development Program from the National Research Foundation of Korea. These initiatives underscore the importance of the project and highlight its potential to drive innovation in advanced manufacturing technologies.
Leave a Reply
You must be logged in to post a comment.