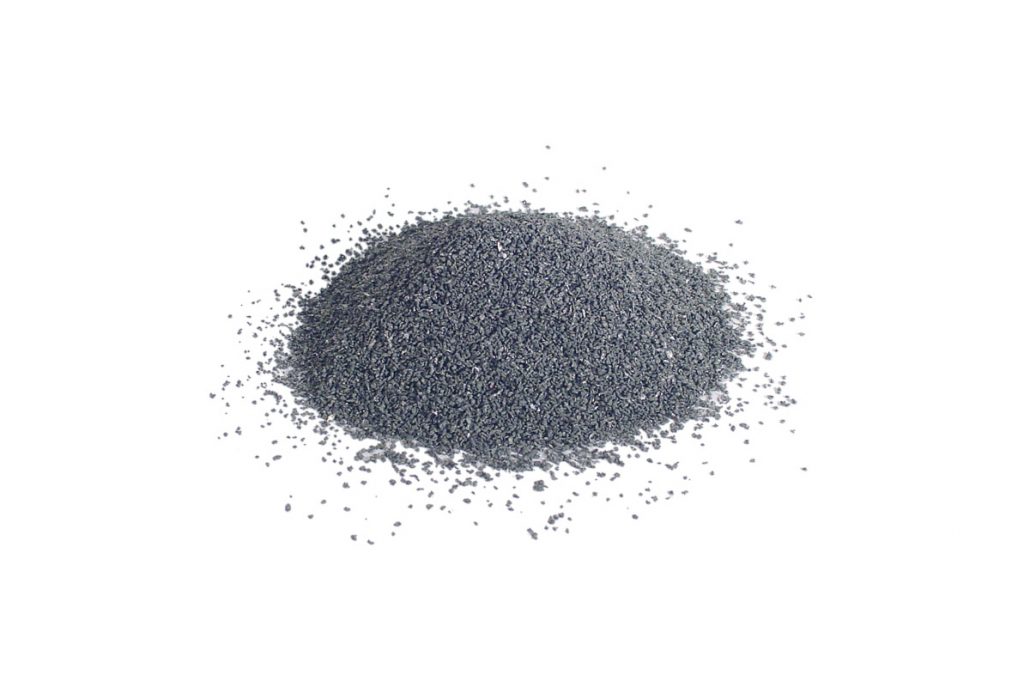
The metal powder market is experiencing an innovative shift. 3D printing’s essential material, metal powder, has traditionally seen limited usability for coarse particles. In Powder Bed Fusion (PBF) processes, only fine particles under 50μm are suitable. Coarse particles, though utilized in Directed Energy Deposition (DED) processes, face limited demand, leading to surplus inventory and significant losses, and inflating the price of powder used in PBF processes. However, a recent breakthrough by the South Korean company Dong-A Special Metal, utilizing plasma melting technology, is disrupting the market by successfully recycling coarse powder into high-quality ingots.
Why Was Coarse Powder (Over 50μm) Discarded?
Metal powder is fundamental in advanced manufacturing, including 3D printing and metal injection molding. However, its usability drastically varies with particle size. While fine powders under 50μm are celebrated for their uniform mixing, excellent sintering, and precise control, coarse powders have been neglected due to several reasons:
- Reduced Surface Area and Reactivity: Larger particles have decreased surface area, diminishing chemical reactivity, impacting performance in applications like catalysts and battery electrodes.
- Difficulties in Uniform Mixing and Dispersion: Coarse particles are harder to mix and disperse uniformly compared to fine particles.
- Sintering and Forming Challenges: Sintering coarse powder leads to lower density and increased porosity, reducing product strength and durability.
- Precision Control Difficulties: In additive manufacturing processes like 3D printing, controlling the interaction between lasers or electron beams and coarse particles is challenging, hindering precise part manufacturing.
Safety Concerns: Some metal powders, when in fine particle form, pose a higher risk of explosion and are more hazardous to human health than coarse particles.
Consequently, up to 70% of coarse powder produced ends up as inventory surplus or scrap.
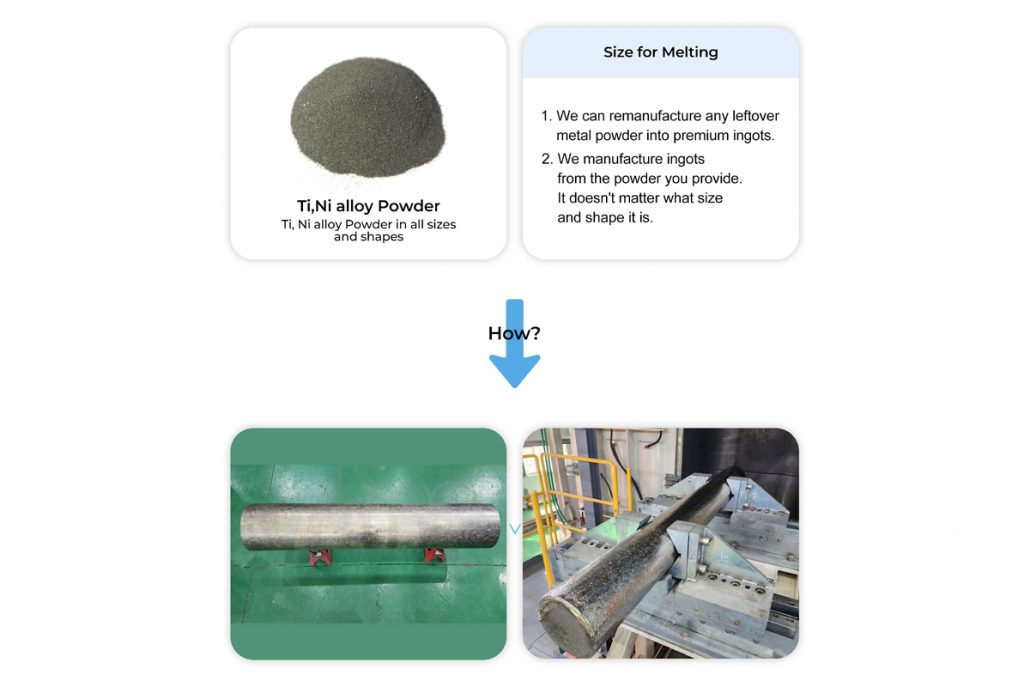
Korean Company Solves the Problem with Plasma Melting Technology
While melting is the sole method to recycle coarse powder, specialty metal powders like titanium and nickel pose significant melting challenges. However, Dong-A Special Metal has developed a process using plasma melting equipment to directly melt specialty metal powders, overcoming these challenges. The resulting ingots have a diameter of 230mm and lengths ranging from 100 to 1,200mm. These ingots can be remade into powder, contributing to a circular economy.
Market Outlook and Competitive Landscape
In the global market, IperionX, a Nasdaq-listed company, leads in metal powder refinement technology, having secured $47.1 million from the U.S. Department of Defense, recognizing its technological prowess. In contrast, Dong-A Special Metal has secured a unique position by possessing the technology to recycle coarse powder into ingots.
Furthermore, Dong-A Special Metal has begun full-scale production of specialty metal ingots using its plasma equipment installed last year, producing diverse products, including Titanium Sponge alternatives, Fe-Ti(Ferro-Titanium), Gr.5, Gr.23, and Ti-15Mo, thereby enhancing its market competitiveness.
Leave a Reply
You must be logged in to post a comment.