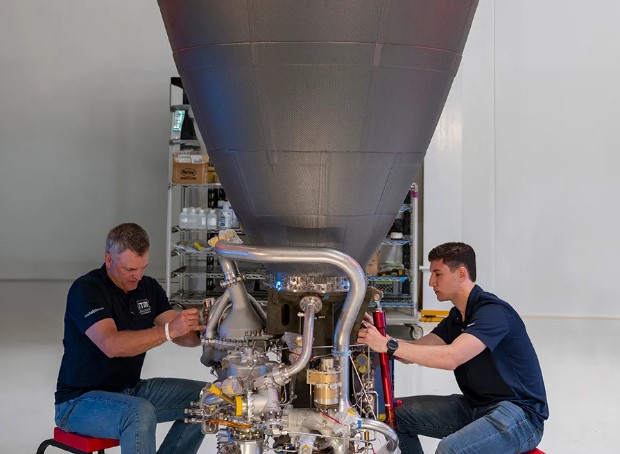
Revolutionizing Rocket Engine Production with Additive Manufacturing
L3Harris Technologies, based in Melbourne, Florida, has successfully delivered its first RL10 engine equipped with an additively manufactured copper thrust chamber to United Launch Alliance (ULA). This milestone highlights the growing role of 3D printing in optimizing the design and manufacturing of high-performance rocket components.
RL10E-1: A Leap Forward in Engine Design and Production Efficiency
The RL10E-1 engine, the latest version of the RL10, features a copper thrust chamber created through Additive Manufacturing (AM). This advancement reduces the number of parts in the thrust chamber by 98%, simplifying design and manufacturing processes. It leads to a significant reduction in production costs and lead times. The RL10E-1 is scheduled to fly aboard ULA’s Vulcan rocket in 2025, cementing its reputation as a reliable, high-performance engine for satellite and spacecraft missions.
Kristin Houston, President of Space Propulsion and Power Systems at Aerojet Rocketdyne, a division of L3Harris, emphasized that 3D printing allows for maintaining high engine performance and reliability while reducing both cost and production time to meet current market demands.
Future of RL10E-1 in ULA’s Vulcan Rocket Program
This successful delivery marks the start of a larger contract with ULA. L3Harris will provide 116 RL10E-1 engines for ULA’s Vulcan rocket program. These engines will deliver about 48,000 pounds of thrust per stage, ideal for precise orbital placements or interplanetary missions. The RL10E-1’s multiple restart capabilities make it an essential component for various space missions.
Leave a Reply
You must be logged in to post a comment.