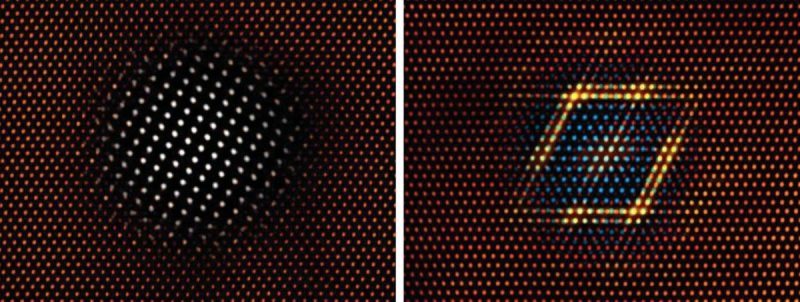
A team of top U.S. researchers has created a copper alloy that redefines performance in high-temperature environments.
The Cu-3Ta-0.5Li alloy resists deformation and coarsening, even when exposed to temperatures close to its melting point.
Developed by Arizona State University, U.S. Army Research Laboratory (ARL), Lehigh University, and Louisiana State University, this alloy brings new strength to copper.
Their work, published in Science, opens doors to next-generation copper-based materials for aerospace, defense, and energy industries.
High Strength, High Heat: Key Properties of the Alloy
This copper-tantalum-lithium alloy remains stable at 800°C (1,472°F) for more than 10,000 hours.
Even under prolonged exposure, it shows minimal yield strength loss.
At room temperature, it achieves a yield strength of 1,120 MPa, exceeding existing commercial copper alloys.
Furthermore, the alloy shows superior resistance to creep deformation.
This makes it a leading candidate for heat exchangers, military-grade electronics, and high-stress aerospace components.
Unique Nanostructure Drives Superior Performance
The alloy’s strength lies in its nanocrystalline structure.
By adding 0.5 atomic percent lithium, researchers altered the copper-tantalum phase behavior.
This shift changed spherical precipitates into stable cuboidal copper-lithium precipitates, surrounded by a tantalum-rich bilayer.
This nanoscale fingerprint boosts both mechanical strength and thermal stability.
As a result, the alloy mimics the strengthening behavior of nickel-based superalloys, but with better conductivity.
Industry Applications and Future Outlook
Although not a full replacement for nickel-based superalloys, this copper alloy provides a strong complementary material.
It suits extreme conditions where both heat resistance and electrical performance are crucial.
Kiran Solanki, a lead author from ASU, says the alloy’s unique structure resists failure caused by heat-induced atomic movement.
By manipulating these “structural fingerprints,” the team achieved a durable, heat-tolerant copper alloy.
Lehigh’s Martin Harmer highlights its potential in hypersonics and advanced turbine engine materials.
Meanwhile, ARL’s Kris Darling sees this as a breakthrough in nanostructured alloy design for harsh environments.
At SuperMetalPrice, we see this as a milestone for copper alloys—particularly those used in high-value industries.
Leave a Reply
You must be logged in to post a comment.