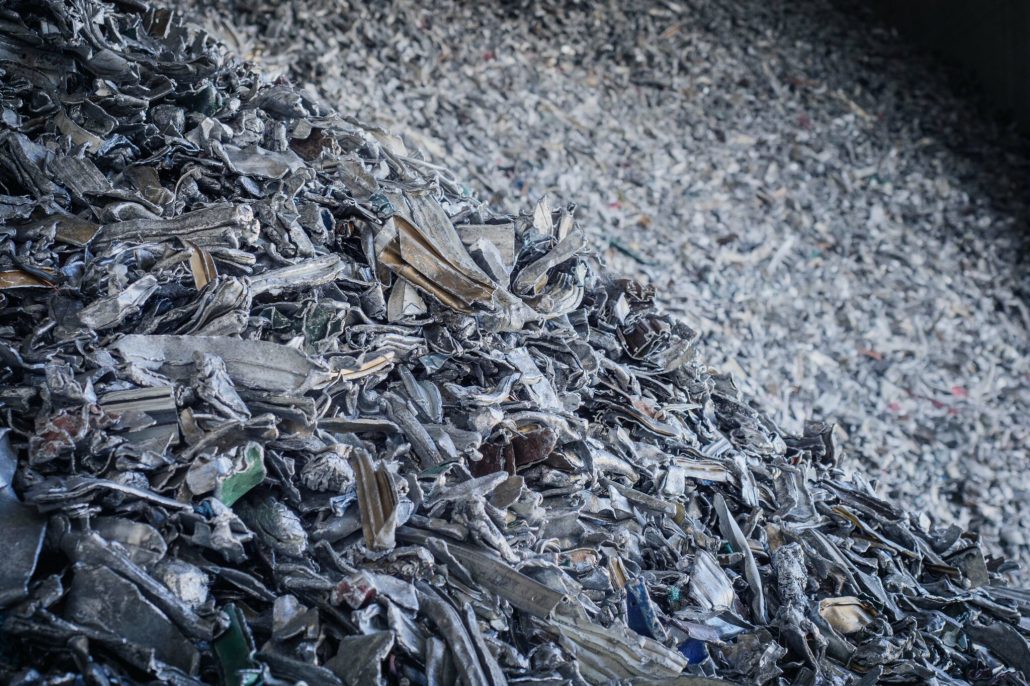
A revolutionary study by the U.S. Department of Energy’s Pacific Northwest National Laboratory (PNNL) introduces a groundbreaking process that transforms aluminum scrap directly into high-performance alloys. This innovation eliminates traditional melting methods, which are energy-intensive and time-consuming. Published in Nature Communications, the new method uses solid-phase alloying to upgrade aluminum waste into high-strength materials. It promises a cost-effective and sustainable solution, with properties comparable to those made from primary aluminum, and could change the aluminum recycling industry.
Solid Phase Alloying: Rapid and Efficient
The solid-phase alloying process uses PNNL’s patented Shear Assisted Processing and Extrusion (ShAPE) technique. This method rapidly converts aluminum scrap combined with metals like copper, zinc, and magnesium into high-strength alloys in under five minutes. Unlike conventional methods that involve melting, which can take days, this process eliminates the need for bulk melting. As a result, it significantly reduces energy consumption and manufacturing time. This breakthrough could lower the cost of producing high-performance aluminum alloys and promote sustainable recycling practices.
Enhanced Material Strength and Sustainability
The alloys created with the ShAPE process are 200% stronger than traditional recycled aluminum. They exhibit superior mechanical properties, including enhanced ultimate tensile strength. This means products made from these alloys could last longer and perform better in demanding applications. The atomic-level features formed during ShAPE, such as Guinier-Preston zones, contribute to the alloys’ improved strength and stability, making them ideal for high-performance industries that require durable materials.
Broad Potential Applications Beyond Aluminum
Although the study primarily focuses on aluminum, the solid-phase alloying process holds potential for other metals. Researchers believe the technique could be applied to various metal combinations, creating alloys previously difficult or impossible to produce. This process can be tailored for specialized applications like 3D printing. In industries such as wire arc additive manufacturing (WAAM), where custom metal wire alloys are essential, precise control over alloy composition could offer significant benefits.
Environmental and Economic Impact
This innovative process significantly reduces the environmental impact of aluminum production. By utilizing aluminum scrap and bypassing melting, it lowers energy consumption. The method also reduces manufacturing costs, making high-quality recycled aluminum alloys more accessible. This advancement supports sustainability in metal recycling and helps industries move closer to achieving net-zero emissions goals, contributing to a greener future.
Leave a Reply
You must be logged in to post a comment.