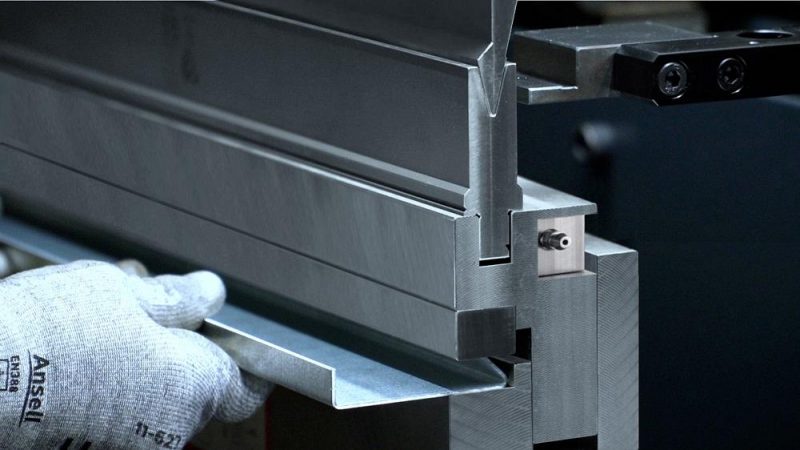
Hemming plays a crucial role in sheet metal fabrication, but if not managed correctly, it can create significant bottlenecks in production. For metal manufacturers, optimizing hemming processes is essential for improving throughput and reducing waste. This article explores efficient strategies for hemming in press brake operations, shedding light on best practices and effective tooling solutions.
Hemming vs. Flattening: Understanding the Difference
Hemming and flattening are often confused, but they are distinct processes with different purposes. According to Steve Brown, bending product manager at Wilson Tool, flattening involves using a heavy hammer toolset to flatten material, while hemming requires a more precise approach with specialized dies. Hemming typically involves creating a small radius at the bend’s edge to prevent material from cracking during further processing.
In the press brake, an acute bend is initially formed before applying additional pressure to create the final hem. Flattening, on the other hand, is performed using a “big hammer” approach, which flattens the hem and can straighten material. The key difference lies in the final result – a hem will have a near-zero inside radius, while a flattened bend appears more compressed.
Tooling Solutions for Efficient Hemming
Selecting the right tooling for hemming is essential to streamline operations and reduce inefficiencies. For shops with high hemming volumes, single-station hemming tools offer a convenient solution. These tools combine all required hits into a single toolset, allowing operators to perform the entire hemming operation with fewer tool changes. Popular designs include spring-loaded mechanisms, which make the process faster and more efficient.
For shorter hems, a combination of acute and flattening dies may work well. However, for longer hems, a flattening die must often replace the acute die, resulting in longer setup times. To address these challenges, operators can use single-station hemming tools that handle both operations seamlessly. These tools, designed for flexibility, are perfect for handling light-gauge material or specific applications like stainless steel.
Challenges with Thicker Material
Hemming thicker materials, such as 12 or 14-gauge metal, introduces additional complexities. A thicker material has a larger outside radius, making it difficult to collapse the hem efficiently. Without sufficient material contact, the hem can “pop out” toward the operator. Special thrust-absorbing dies can help mitigate this problem by absorbing excess force during the flattening process. As Vander Wall from WILA USA mentions, thick materials, like 12-gauge stainless, require tools that can accommodate the increased force generated during the flattening process.
Avoiding Cracks in Hard Metals
Another challenge with hemming is preventing cracking in hard materials like 6061-T6 aluminum or certain stainless steel alloys. Hemming these materials requires precision, as they are prone to cracking under stress. One effective strategy is to create a teardrop hem, which helps reduce the likelihood of cracking by providing edge protection and using lower tonnage. As Larry Boden of Mate Precision Technologies points out, proper tool selection and technique, such as backing off slightly during the flattening process, is crucial to avoiding material failure.
Horizontal Hemming for Large Panels
For shops dealing with large panels, horizontal hemming offers an efficient solution. With this technique, the material remains flat during the entire hemming process, reducing the need for operators to lift large panels or bend them manually. Special flat-sheet hem tools use a wiping action to form the initial acute flange and complete the final hem shape. This approach ensures a more consistent hem and can be adapted to specific material requirements.
Conclusion: Finding the Right Tool for the Job
The success of any hemming operation depends on selecting the right tool for the specific material, part size, and volume. For shops struggling with hemming inefficiencies, investing in specialized tooling can significantly improve production flow. Whether through single-station tools, thrust-absorbing dies, or horizontal hemming solutions, there are various strategies to optimize the press brake for faster, more efficient hemming operations.
By addressing common issues like tooling changes, material thickness, and part size, metal fabricators can improve both the speed and quality of their hemmed parts, ensuring a smoother workflow and better overall performance.
Leave a Reply
You must be logged in to post a comment.