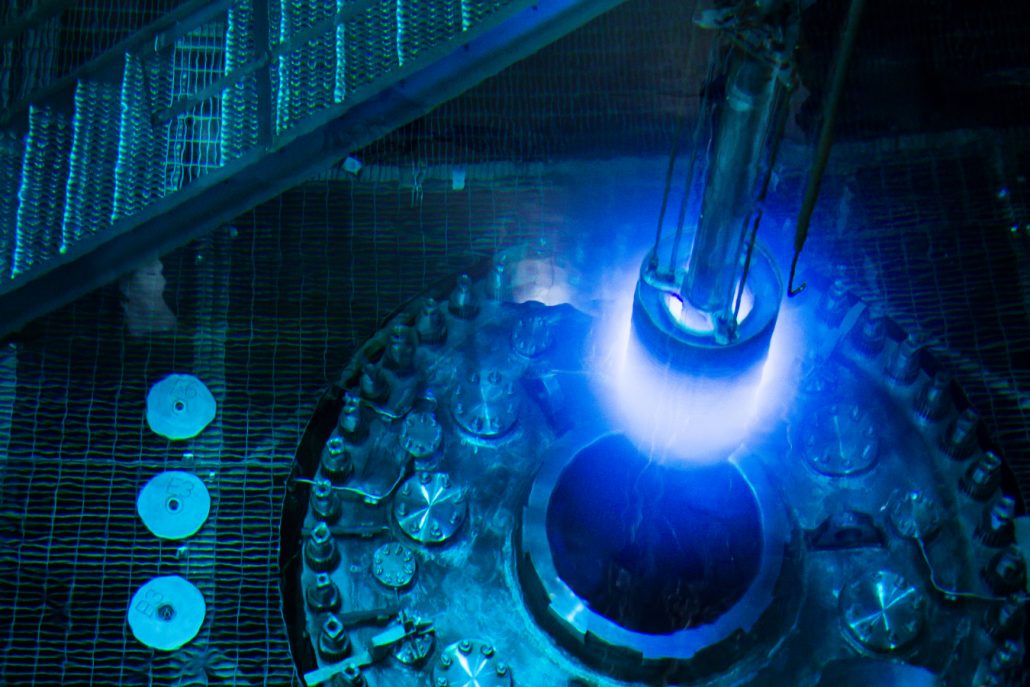
지게리지 국립연구소의오레곤 국립미국 테네시주에서는 고플럭스에 대한 동위원소 반응기(High Flux Isotope Reactor)에서 사용하기 위해 실제로 제조된 패치를 성공으로 설계하고, 제조 및 테스트함으로써 핵 연구 분야에서 중요한 이정표를 회의했습니다.적외선 카메라). 이 기술은 제조 기반(AM)을 사용하여 제품을 생산한 최초의 생일입니다.토끼 캡슐핵연료 및 재료 연구의 필수 구성 요소입니다.
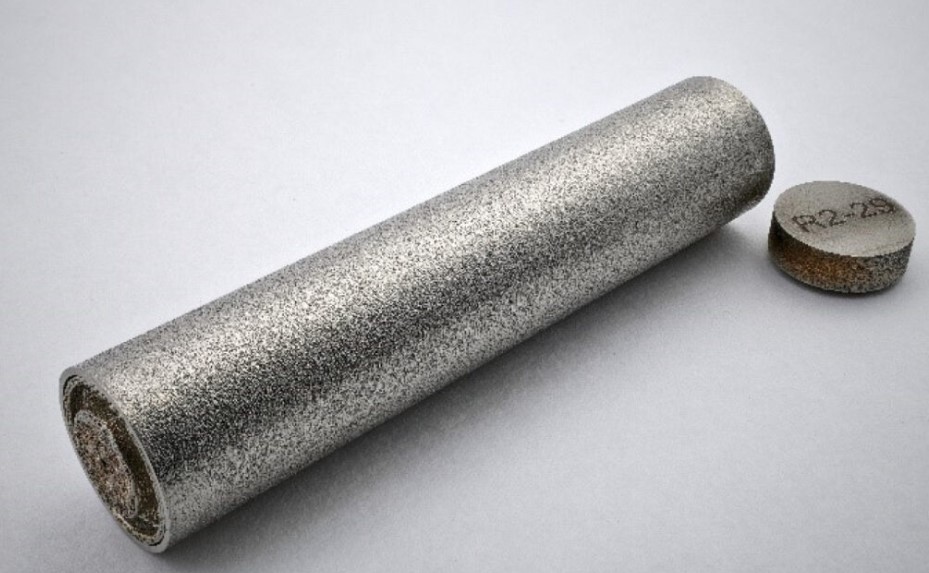
고중성자 플럭스 원자로 환경 테스트
그만큼귀체캡슐토끼 패치로 패치는 시험 반응기에서 조사를 대상으로 실험을 보관하는 데 사용됩니다. AM의 잠재력을 증명하기 위해e=”vertical-align: 의심스러운;”>핵무기프로그램에서 ORNL은 알파 쿠션(Laser Beam Powder Bed Fusion)을 적용했습니다.tyle=”vertical-align: 겁쟁이;”> PBF-LB)오전스테인레스 스틸 패치를 제조하는 기계입니다. 이 조립은 조립되어 있으며, 벽돌한 다음 HFIR 내부의 고중성자 플럭스 환경에 거의 한 달 동안 계속되었습니다. 당신은 혹로의 혹독한 힘을 성공시켰습니다.
ORNL의 파트너링 그룹 리더인 Richard Howard는 이 성과의 분할을 강조하며, “이것은 기반화된 기술을 사용함으로써 기존 방식을 견딜 수 없는 부품을 개발하고 적격성을 평가할 수 있다는 것을 보여주는 중요한 단계입니다.”라고 말합니다.
ORNL의 시연 시설을 요구하는 사항인 라이언 데호프는 테스트의 더 광범위한 의미를 강조하며 “이러한 인쇄 구성 요소의 인증을 인증함으로써, 우리는 적층된 다른 중요한 원자로 부품을 생산하는 기준이 될 것을 기대하고 있습니다.”라고 합니다.
<div class=”wp-block-spacer” style=”높이: 10px;” aria-hidden=”true”>
미래의 핵 응용 분야를 전투하는 길을 개척자 하
다
스위치 테스트에 이어 ORNL은 패치의 성능을 더욱 평가하기 위해 조사 후 평가를 수행할 계획입니다. 이 응용 분야에서 AM을 성공으로 사용하면 핵 에너지 부품과 기타 구성 요소가 산업에서 안전에 중요한 구성 요소에 AM 기술을 장착하는 것이 맞을 수 있을 것으로 예상됩니다. 교체는 AM의 설계로 기초를 활용하여 기본 방식으로 제작하기 위해 최적화된 구성 요소를 만드는 것을 목표로 합니다.
이 연구는 새로운 구성원과 제조 기술의 구성원화를 발전시키는 데 알리고 미국 에너지부의 구성원 및 기술 프로그램의 지원을 위해 사용되었습니다.
Leave a Reply
You must be logged in to post a comment.