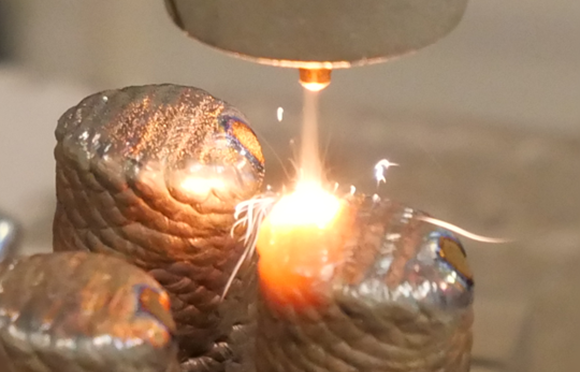
Introduction: Advancements in Titanium Additive Manufacturing
Oscar-PLT GmbH from Klipphausen, Germany, and m4p material solutions GmbH from Magdeburg have made significant progress in titanium additive manufacturing. They recently collaborated on a project to produce Ti-6Al-4V components using the ProFocus Directed Energy Deposition (DED) technology. This represents a major advancement in the additive manufacturing of high-performance titanium alloys.
ProFocus DED Technology: Key Features and Benefits
The ProFocus machine features six individually controllable lasers surrounding a central metal feedstock, either in powder or wire form. This setup allows precise control over the energy input and a uniform distribution of heat. Oscar-PLT claims this control enables the processing of materials that were previously challenging. The ProFocus system also operates without requiring an enclosed space, thanks to its shielding gas flow. This offers increased flexibility for various industrial applications.
At the recent additivefertigung: metal in bestForm conference, Dr. Michael Schnick from Oscar-PLT and Dr. Burghardt Klöden from m4p presented their findings. Dr. Schnick focused on the technology behind the ProFocus DED and wire processes, while Dr. Klöden explained the properties achievable with m4p’s Ti-6Al-4V powder (Ti grade 23.09).
High-Performance Titanium Components with Ti-6Al-4V Powder
The results were noteworthy. Dr. Klöden explained that the mechanical properties of the components made with m4p’s Ti-6Al-4V powder matched those typically found in titanium alloys processed via Laser Beam Powder Bed Fusion (PBF-LB) Additive Manufacturing. This confirms that ProFocus DED technology is compatible with Ti-6Al-4V powder, which is widely used in aerospace, medical devices, and high-performance engineering applications.
This breakthrough enables industries to produce high-strength, lightweight materials more efficiently. The ability to process Ti-6Al-4V with ProFocus DED technology allows manufacturers to create titanium components with superior mechanical properties.
Conclusion: A Breakthrough in Titanium Additive Manufacturing
The collaboration between Oscar-PLT and m4p material solutions demonstrates a significant advancement in titanium alloy production using additive manufacturing. The ProFocus DED system, combined with m4p’s Ti-6Al-4V powder, allows the creation of components with mechanical properties previously achievable only through traditional methods. This innovation sets the stage for more efficient production of critical components across industries like aerospace, automotive, and medical fields.
Leave a Reply
You must be logged in to post a comment.