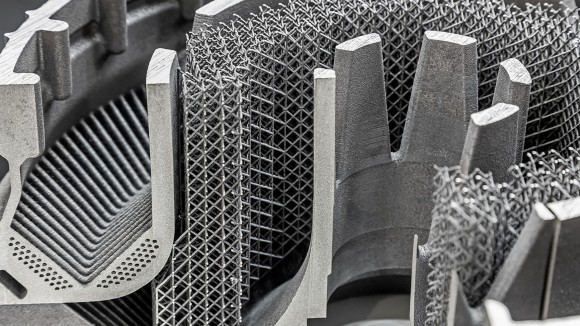
Researchers from the University of Toronto have developed a new strategy to control microstructure in Laser Beam Powder Bed Fusion (PBF-LB) additive manufacturing. Their method manipulates the overlap of melt pools to influence grain structure, without altering typical energy densities or scan patterns. Published in Scripta Materialia, this innovative approach has great potential to improve material properties in various additive manufacturing (AM) applications.
Controlling Grain Structure in Stainless Steel
In the study, the researchers used 316L stainless steel as a model material. They found that adjusting the overlap of melt pools affects the size and morphology of the grains. When the melt pools overlap, the extent of overlap determines whether new grains are retained or eliminated. The study reveals that grain nucleation mainly occurs at the free surfaces of the melt pool boundaries. This discovery offers a new method for controlling grain size and distribution in PBF-LB metal parts.
Broader Impact for Metal Alloys and Additive Manufacturing
This strategy is versatile and can be applied to many metallic alloys. By adjusting the overlap of melt pools, manufacturers can influence material properties in the final product. This method enables the optimization of metal parts for use in industries such as aerospace, automotive, and biomedical fields. It provides a powerful tool for achieving specific mechanical properties in AM-produced metal parts, enhancing the capabilities of current AM processes.
Study Implications and Future Research Directions
This breakthrough in remelting-based microstructure engineering is a significant step forward in material customization for additive manufacturing. The study highlights how controlling melt pools during printing can improve material properties. Future research will focus on refining this method for a wider range of materials and exploring its potential in other AM technologies.
Leave a Reply
You must be logged in to post a comment.