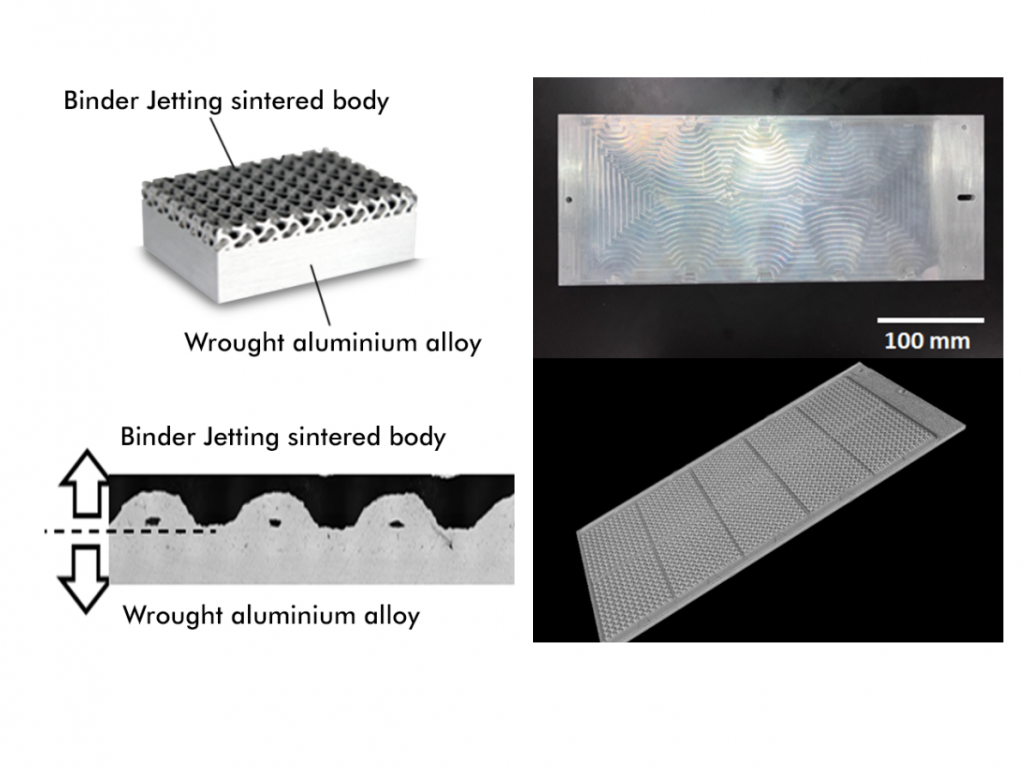
Indeed, Ricoh Company, Ltd., a frontrunner in technological innovation, has recently unveiled a novel diffusion bonding technology. This advancement, notably, significantly enhances the process of joining aluminum parts. Specifically, these parts are fabricated using Binder Jetting (BJT) and then bonded to wrought aluminum alloys. Consequently, this innovative technique not only facilitates the production of larger components but also, importantly, promises a substantial reduction in manufacturing costs.
Innovating Beyond Traditional BJT Limitations Through Diffusion Bonding
Metal Binder Jetting (BJT), primarily recognized for its cost-effectiveness, also stands as a high-productivity Additive Manufacturing technology. Therefore, it proves exceptionally suitable for both rapid prototyping and efficient mass production. Nevertheless, a significant challenge persists: achieving precise dimensional accuracy with larger parts. Particularly, this challenge arises due to the inherent complexities of the sintering process.
To directly address this issue, Ricoh’s diffusion bonding technology skillfully employs a proprietary liquid-phase sintering method. In particular, this process enables the seamless integration of sintered aluminum BJT parts with conventional wrought aluminum alloys, including widely used alloys like 6061 and 1050. Furthermore, this innovative bonding technology offers distinct advantages for applications such as high-efficiency heat exchangers, where, crucially, both intricate geometries and precise dimensional accuracy are indispensable.
For example, a key application involves the fabrication of intricate fins using BJT. Subsequently, these fins are bonded to an aluminum case, which itself is manufactured through traditional methods. As a result, the final component delivers significantly enhanced cooling performance, primarily attributed to the sophisticated complex fin shapes. Additionally, the component maintains its dimensional integrity, largely due to the high machining accuracy of the case.
Unlocking Potential for Larger Components and Substantial Cost Reduction
Moreover, Ricoh’s new diffusion bonding method has undergone rigorous testing with components like a large cooling part, which measured 400 mm x 160 mm x 10 mm. This advanced bonding process, when combined with brazing, allows production of large components. Previously, BJT alone struggled to manufacture such parts.
Additionally, Ricoh’s technology showcases broad compatibility with various aluminum alloys, including the versatile 6063 alloy. Furthermore, it has demonstrated effective performance across both the BJT fabrication and bonding processes. Ultimately, this significant innovation is poised to bring about considerable cost reductions in manufacturing. Also, it will enable the production of larger, more complex components than ever before.
Takafumi Sasaki, the head of Ricoh’s metal BJT project, notably underscored the significant advantages of this pioneering technology. Indeed, he explicitly stated that it would substantially enhance cooling efficiency, significantly reduce costs, and, equally importantly, facilitate the manufacturing of larger component sizes. In the future, Ricoh intends to further explore the practical feasibility of these advancements in real-world applications by engaging in collaborative partnerships with its customers.
Leave a Reply
You must be logged in to post a comment.