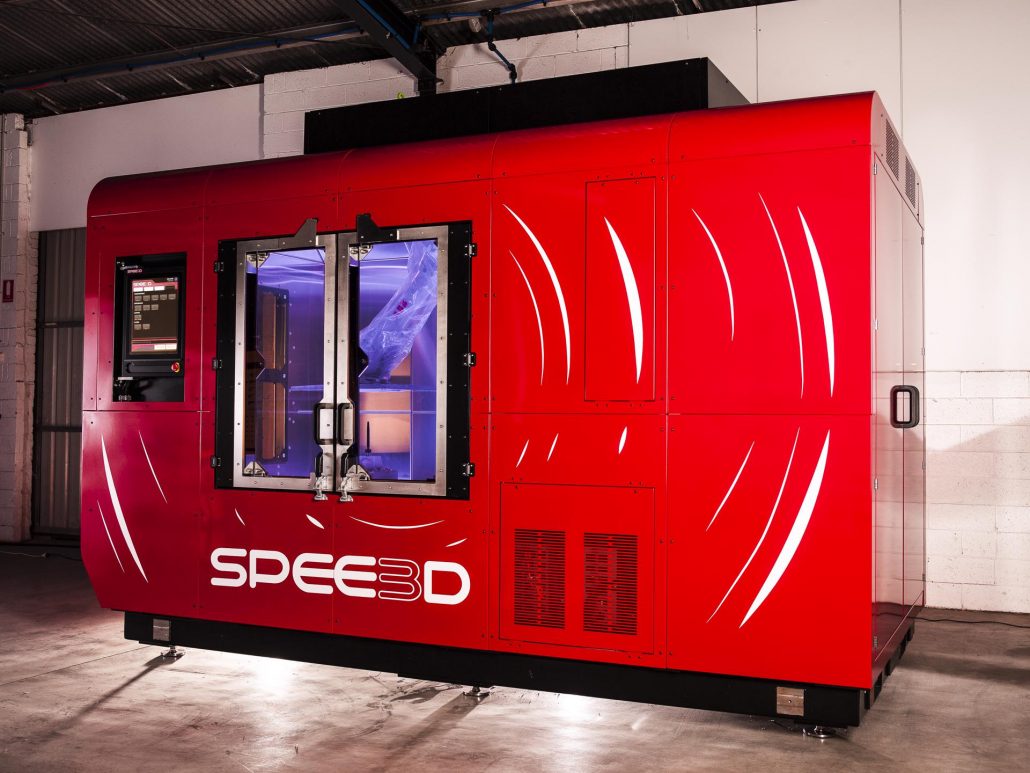
SPEE3D has achieved a major breakthrough. They successfully demonstrated their XSPEE3D machine’s ability to operate in sub-zero conditions. Impressively, this machine produces metal parts. Material properties match those made in controlled labs. This achievement showcases the machine’s robustness. Moreover, it meets the rising demand for advanced manufacturing in harsh environments.
Notably, US Department of Defense Collaboration Spurs Cold-Weather Manufacturing Success
SPEE3D partnered with the US Department of Defense (DOD). Specifically, they collaborated with the New Jersey Institute of Technology (NJIT) COMET Project and Philips Federal. The US Army’s Cold Regions Research and Engineering Laboratory (CRREL) then hosted the challenge. Consequently, the XSPEE3D machine successfully manufactured critical components. It created battle damage repairs and large metal parts on-demand in frigid conditions.
Furthermore, XSPEE3D Displays Unmatched Versatility Across Extreme Climates
SPEE3D’s Cold Spray technology previously proved effective in hot environments. The Australian Army, for instance, tested it in the Australian bush. Now, it has succeeded in sub-zero temperatures. Therefore, the XSPEE3D machine adapts to numerous environmental conditions. This versatile technology supports military and industrial needs. It functions in remote, cold regions and harsh, hot climates. As a result, it reduces reliance on supply chains. It enables on-site manufacturing. SuperMetalPrice considers this a substantial advancement in metal fabrication.
Consequently, Cold Spray Manufacturing Significantly Impacts Military and Industrial Operations
SPEE3D’s Cold Spray Metal Additive Manufacturing bolsters the DOD’s expeditionary manufacturing goals. It produces high-quality parts on-demand. Indeed, this technology closes crucial supply chain gaps. It provides soldiers with necessary tools. Byron Kennedy, CEO of SPEE3D, stressed the machine’s ability to print metal parts anywhere, regardless of weather.
Ultimately, Future Prospects Brighten for Cold Spray Technology and Technological Innovation
SPEE3D continues to expand its Cold Spray technology applications. It establishes itself as a leader in additive manufacturing. This applies especially to industries needing rapid, reliable manufacturing in remote locations. The trial reinforces additive manufacturing viability. It supports critical operations in challenging environments. SPEE3D’s work strengthens the US military’s technological edge. It showcases on-site, on-demand manufacturing potential across various industries.
Leave a Reply
You must be logged in to post a comment.