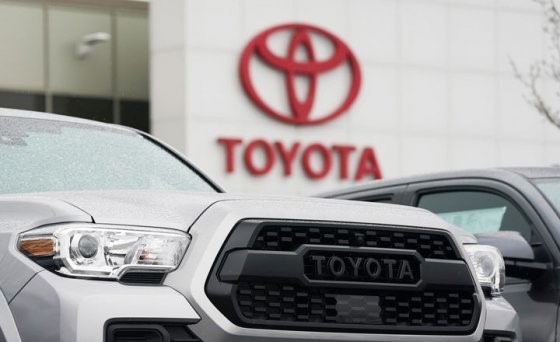
Toyota Engineering & Manufacturing North America Inc. (TEMA) has received a $4.5 million grant from the U.S. Department of Energy’s Advanced Research Projects Agency-Energy (ARPA-E). This funding supports the development of a domestic circular supply chain for electric vehicle (EV) batteries. Part of the Catalyzing Innovative Research for Circular Use of Long-lived Advanced Rechargeables (CIRCULAR) program, the project focuses on sustainable solutions for reusing and recycling EV batteries, enhancing battery lifecycle management, and reducing waste in the EV industry.
Collaborative Effort to Enhance EV Battery Sustainability
The project, led by Toyota’s Research Institute of North America (TRINA), will partner with Oak Ridge National Laboratory (ORNL), the National Renewable Energy Laboratory (NREL), and Baker Hughes’ Waygate Technologies. The initiative’s goal is to create a 3R (Reduce, Reuse, Recycle) facility that will address challenges in the EV battery supply chain, specifically focusing on EV battery recycling. This includes automating battery pack disassembly, improving battery classification with data-driven methods, and solving issues like cell degradation. These advancements are vital for prolonging the lifespan of batteries and boosting their reuse before recycling, promoting more efficient EV battery recycling practices.
Innovations in Battery Disassembly and Classification
A key part of the project is developing automated processes for EV battery pack disassembly. These innovations aim to improve efficiency in extracting reusable battery cells and components. New diagnostic tools will classify battery modules and cells to assess their remaining lifespan and performance. By optimizing these processes, the project aims to reduce the environmental impact of battery waste and encourage a more sustainable, circular approach to EV battery manufacturing.
Toyota’s Vision for Sustainable Mobility
This project aligns with Toyota’s commitment to sustainable mobility solutions. By focusing on reducing battery waste and improving the circularity of the EV battery supply chain, Toyota is advancing toward a more eco-friendly future. The findings from this project will be implemented by Toyota’s Battery Lifecycle Solutions (BLS) team to create a sustainable framework for managing EV battery lifecycles and reducing the environmental footprint of battery production.
Leave a Reply
You must be logged in to post a comment.