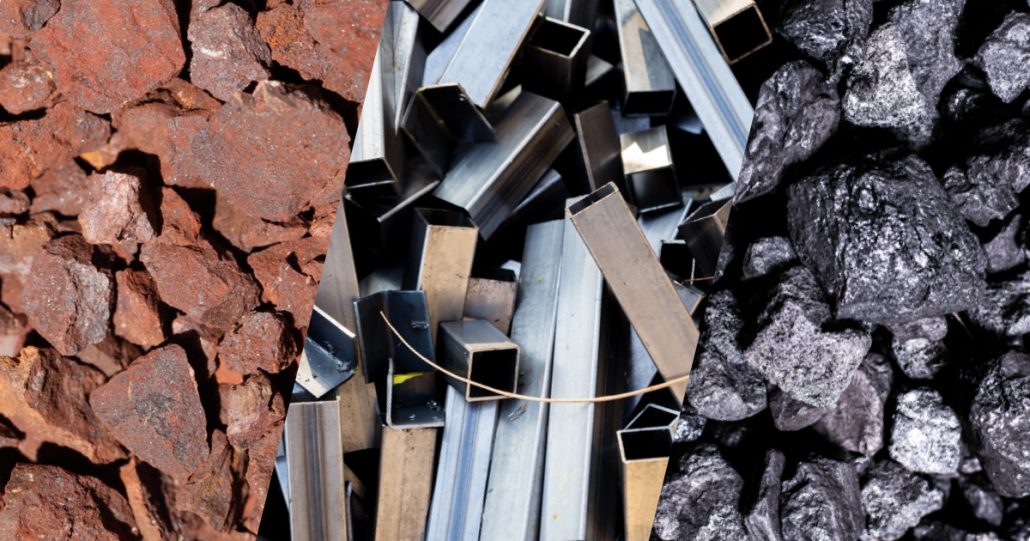
Raw Material Costs at the Forefront
In the metal fabrication industry, raw materials represent the largest expense. As purchasing teams navigate the complexities of pricing, weight, and payment terms, they must also consider market fluctuations and mill utilization rates. Misunderstandings in purchasing terminology can lead to hidden costs that impact profitability.
Calculating Weight Accurately
Weight calculations in metal purchases can vary significantly based on the transaction terms used, such as actual weight versus theoretical weights. For example, a buyer purchasing hot-rolled steel must be aware of the differences between nominal and actual thickness, which can influence pricing. Understanding these distinctions is crucial for effective cost management.
Risks of Overseas Sourcing
Buyers often pursue lower-cost options from international suppliers, but this can introduce unique financial risks. Shipment delays, influenced by global events like pandemics or geopolitical tensions, can lead to increased costs and cash flow issues. Proper planning and safety stock can mitigate these risks, but buyers must also remain aware of changing regulations and potential tariffs, especially during election years.
Importance of Shipping Terms
Shipping terms significantly affect costs and risks in international transactions. The use of Incoterms, which outline the responsibilities of buyers and sellers, is essential for preventing misunderstandings. Each term, from EXW to DDP, defines who bears the risks and costs associated with transport, highlighting the need for precise communication in international dealings.
Limitations of Economic Order Quantity (EOQ)
While the EOQ formula helps determine optimal inventory levels, it often oversimplifies the complexities of fluctuating market conditions. Regular recalibration is necessary to align with actual demand and changes in holding costs. Additionally, minimum order quantities (MOQ) imposed by suppliers can impact purchasing decisions, requiring careful negotiation.
Beyond Price: A Comprehensive Approach
Effective purchasing strategies extend beyond merely negotiating price per pound. They encompass considerations of order quantity, sourcing location, and cash flow impacts. By examining the intricate details of agreements, buyers can uncover potential savings and more favorable terms, ultimately enhancing profitability in the metal fabrication sector.
Leave a Reply
You must be logged in to post a comment.