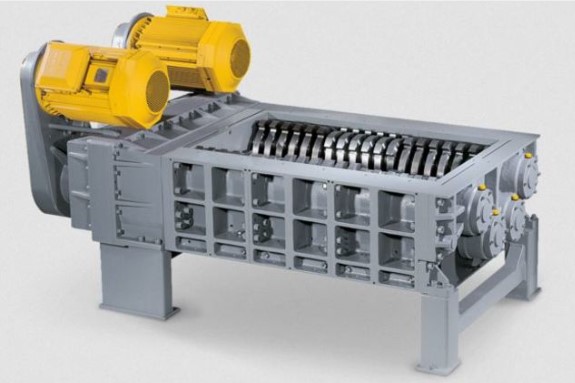
Proficio Ltd., based in Livingston, England, has recently upgraded its metal recycling and purification operations. The company installed an Untha RS50 four-shaft shredder to improve its processing capabilities. Known for its experience in decontaminating scrap metal turnings and superalloys, Proficio handles materials commonly used in aerospace applications, including alloys with iron, nickel, cobalt, and other metals. This new shredder increases the company’s efficiency in handling metal turnings, helping Proficio meet the growing global demand for remanufactured materials.
Efficient Shredding Capabilities for Increased Throughput
The RS50 shredder significantly boosts Proficio’s capacity. It can shred 1,100 to 1,700 kilograms (2,425 to 3,750 pounds) of metal turnings per hour. The machine reduces materials to 20mm (¾ inch) chips, perfect for cleaning and improving shipping density. The shredder’s interchangeable screen allows Proficio to control the output size in a single pass, optimizing efficiency and eliminating additional steps in the shredding process.
Investing in Growth and Technological Advancements
The addition of the RS50 shredder aligns with Proficio’s long-term growth strategy. With this new technology, the company aims to double its processing capacity over the next three years. Mark Semple, Proficio’s Managing Director, emphasized that the investment in the shredder was essential for increasing throughput. He believes the decision, despite the initial challenges, has already proven beneficial for the company.
Customer Research and Untha’s Reputation for Quality
Before making this investment, Semple conducted thorough market research and spoke with industry peers who had experience with Untha shredders. Positive feedback from these peers, particularly about the RS50, played a key role in the decision. Semple was impressed with the consistent chip quality produced by the shredder after visual inspections. Additionally, Untha supported Proficio with detailed user training and a two-year service plan to ensure optimal machine performance.
Leave a Reply
You must be logged in to post a comment.