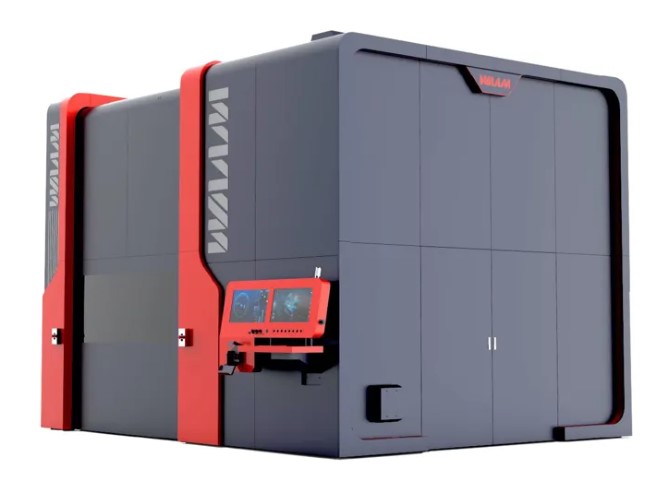
WAAM3D, a UK-based additive manufacturing company, has introduced its most advanced machine yet, the RoboWAAM XP, at Formnext. This new system builds on the company’s line of integrated advanced manufacturing solutions and offers expanded size and mass capabilities. The RoboWAAM XP is designed to meet the growing demand for large-scale parts in industries such as energy, space, marine, and mining. The system is based on the Cold-Wire Gas Metal Arc (CWGMA) process, developed by Cranfield University, which provides high deposition rates and the ability to work with a wide range of materials.
Cold-Wire Gas Metal Arc Technology for High Efficiency
The key innovation behind the RoboWAAM XP is the Cold-Wire Gas Metal Arc (CWGMA) process. This process involves the integration of a non-energized cold wire with the conventional Gas Metal Arc (GMA) process, allowing for more efficient material deposition. The system can achieve deposition rates of up to 15 kg per hour, nearly doubling the material output for the same energy input. Stewart Williams, Technical Director at WAAM3D, explained that this innovation not only enhances the deposition efficiency but also stabilizes the process, making it suitable for a broader range of materials, including iron, aluminum, nickel, and copper alloys. Furthermore, the ability to precisely control the process opens up the possibility of tailoring microstructures to achieve desired material properties.
Key Features and Capabilities of the RoboWAAM XP
The RoboWAAM XP features a maximum build envelope of 2 x 2 x 2 meters, offering the flexibility to manufacture large parts. It can handle a maximum payload of 2.1 tonnes, making it suitable for heavy-duty applications. The system utilizes a 6-axis robotic arm and a 2-axis part rotator, achieving a high level of precision with robot repeatability of ±0.05mm. The machine is equipped with MIG, MAG, and CMT welding technologies from Fronius, which ensures versatility in material handling. Additionally, the RoboWAAM XP incorporates WAAM3D’s software solutions, WAAMPlanner and WAAMCtrl, which streamline the workflow, from build setup to laser calibration, ensuring high-quality results.
Applications and Testing in Key Industries
Over the past two years, WAAM3D has tested the RoboWAAM XP across various industries. These include energy, space, marine, and mining. These sectors require the production of large, complex components. The RoboWAAM XP excels in high productivity, precision, and material versatility. As a result, it is perfect for these demanding applications. Dr. Jialuo Ding, CTO at WAAM3D, highlighted that the RoboWAAM XP meets stringent quality standards. He called it a “pivotal moment in the industry.” The high productivity of this system will support the growing needs of these sectors.
MiniWAAM: Smaller Scale, Same Innovation
In addition to the RoboWAAM XP, WAAM3D also launched the MiniWAAM earlier in the year. This smaller version of the flagship RoboWAAM product provides a compact and cost-effective solution for industries requiring smaller-scale additive manufacturing. The MiniWAAM was showcased at the TCT 3Sixty event, offering a glimpse into WAAM3D’s broader range of additive manufacturing solutions.
Leave a Reply
You must be logged in to post a comment.