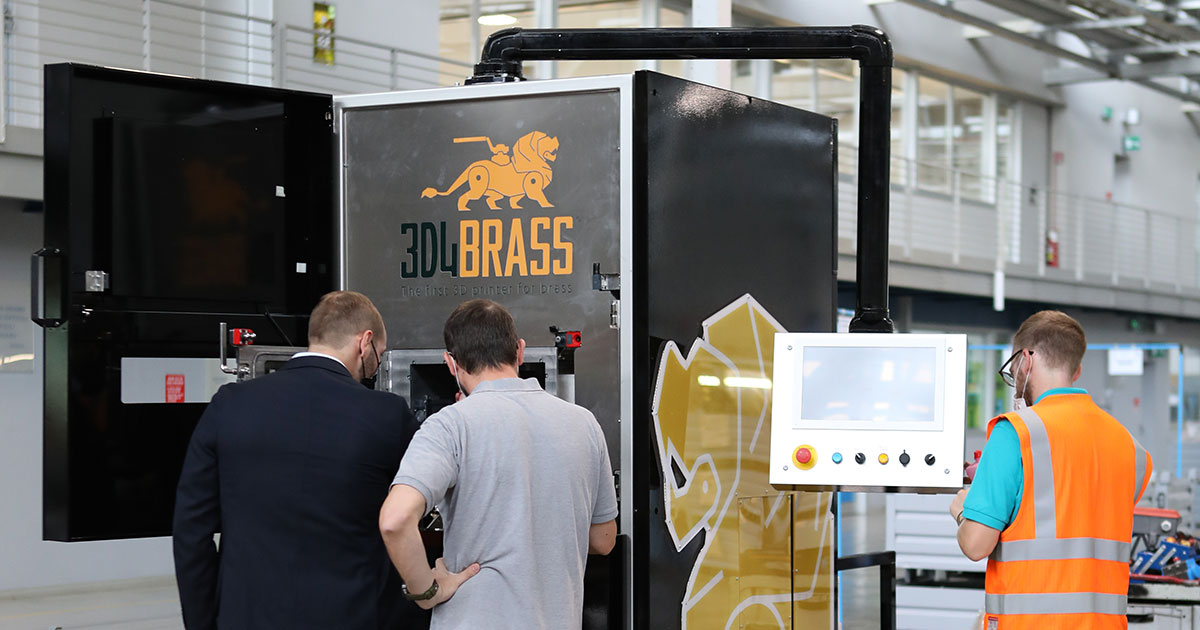
Italian additive manufacturing firm 3D4MEC has teamed up with the Fraunhofer Institute for Additive Manufacturing Technologies IAPT to develop an in-situ optical monitoring system for its innovative 3D4BRASS 3D printer. This initiative seeks to enhance the stability and reliability of printing with brass, a complex material, through real-time monitoring and corrections.
Advancing Brass 3D Printing Capabilities
The 3D4BRASS machine is touted as the only additive manufacturing system capable of processing brass, and this collaboration aims to refine its performance. Testing specialist Thetascan GmbH will contribute by providing an optical system to explore the capabilities of advanced 3D Optical Tomography (3D-OT), enhancing the overall effectiveness of the printing process.
Commitment to Research and Development
Fabrizio Marino Corsini, Managing Director of 3D4MEC, emphasized the importance of this collaboration, stating, “The partnership with Fraunhofer IAPT and Thetascan presents a tremendous opportunity for us to bolster our commitment to research and development, which has seen significant investment in recent years.” The goal is to create customized additive manufacturing solutions tailored to the specific needs of clients and market demands.
Real-Time Defect Detection
The proposed in-situ monitoring system is designed to detect real-time defects during the selective laser melting process, aiming to minimize waste in production. Dennis Jutkuhn, scientific assistant for In-situ Monitoring & Process Control in Laser Powder Bed Fusion at Fraunhofer IAPT, noted, “In 3D4MEC, we have found an excellent partner to advance the development of optical tomography technology. By integrating extended sensor capabilities and fusing multiple sensing technologies, we aim to enhance data-driven quality control in Laser Powder Bed Fusion.”
Continuing Industry Trends
This collaboration aligns with a broader trend in the additive manufacturing sector, where companies are increasingly focusing on quality control solutions. Recent partnerships include Additive Industries joining forces with Additive Assurance to enhance process monitoring for metal 3D printed parts and EOS integrating Oqton’s Build Quality suite for improved traceability of 3D printed components.
Leave a Reply
You must be logged in to post a comment.