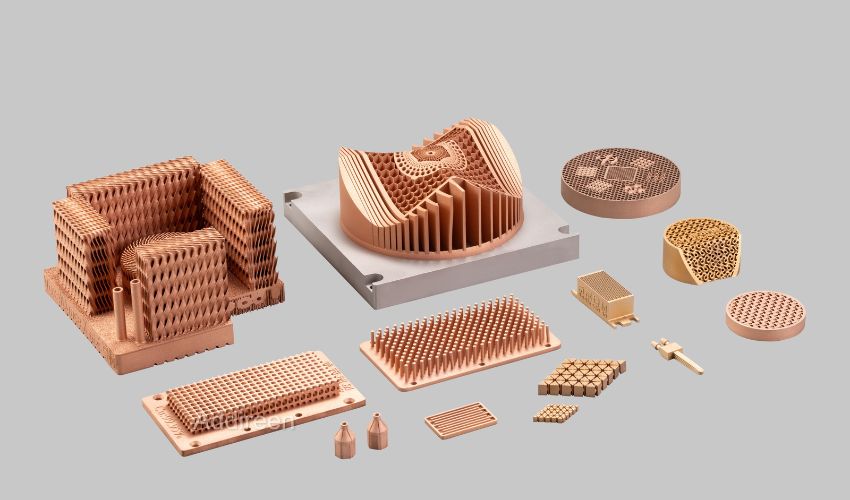
Researchers have achieved a breakthrough in additive manufacturing (AM). Using green lasers, they produced 99.9% dense pure copper parts. This improves the Laser Beam Powder Bed Fusion (PBF-LB) AM process.
Green Lasers Enhance Efficiency
Green lasers offer advantages for processing copper. They have a high absorption rate. This improves printing efficiency and reduces spattering. The study used an AM machine with a 500 W green laser. Researchers optimized parameters like scanning speed. This resulted in copper components with excellent density and conductivity.
Green-Laser AM Machines for Diverse Applications
Addireen offers green-laser AM machines. These machines produce parts from copper and other reflective metals. Examples include gold and silver. The machines feature high-power lasers for precise control. Components made with these machines have high thermal conductivity. They can also withstand high pressure. This makes them suitable for industries like aerospace and new energy vehicles.
Leave a Reply
You must be logged in to post a comment.