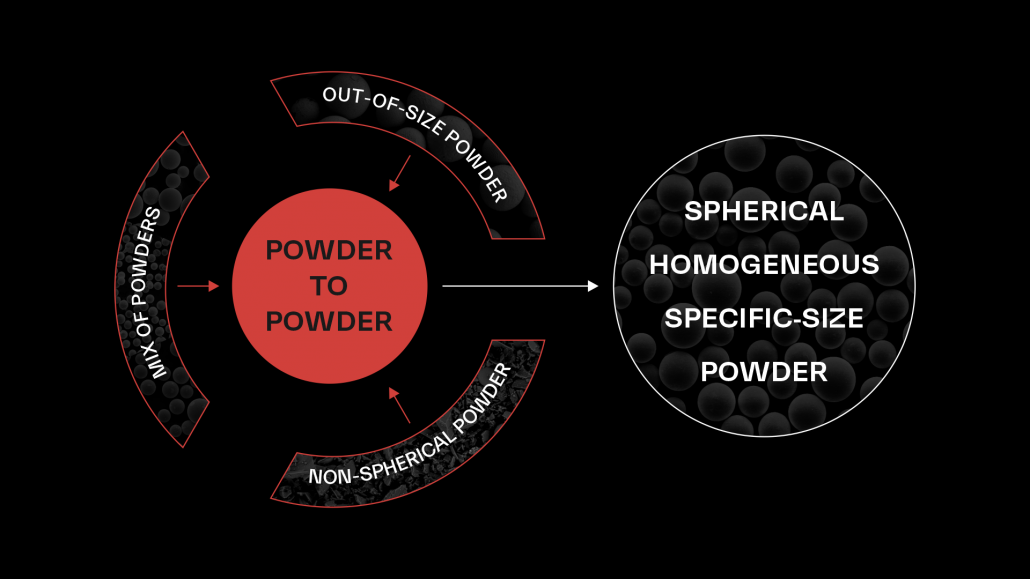
Innovative Technology for Metal Powder Recycling and Custom Alloy Production
Amazemet, a Warsaw-based Polish company, will introduce its groundbreaking Powder2Powder (P2P) atomisation system at Formnext 2024. This system provides a versatile solution for recycling metal powders and producing custom alloy powders directly from feedstock. The P2P system integrates plasma processing and ultrasonic atomisation to convert oversized or irregular metal powders into highly spherical, satellite-free particles optimised for Additive Manufacturing (AM).
Unlike traditional plasma spheroidisation, P2P allows powder size control independent of feedstock. This enables the direct atomisation of pulverised titanium, a process not possible with conventional methods.
Łukasz Żrodowski, CEO of Amazemet, stated: “The Powder2Powder system is a leap forward in powder recycling. It not only addresses the issue of powder waste but also enables manufacturers to customise powder compositions, enhance sphericity, and optimise particle size distribution—critical factors in the AM industry.”
Key Benefits for Additive Manufacturing (AM)
The P2P system has demonstrated outstanding results in titanium (Ti) alloy powder trials, achieving:
-
40 kHz frequency operation for consistent powder refinement.
-
Aspect ratio (D50) exceeding 0.95 and D90 < 80 µm for precise particle size distribution.
-
97% of the output powder suitable for Laser Beam Powder Bed Fusion (PBF-LB), Directed Energy Deposition (DED), and Electron Beam Powder Bed Fusion (PBF-EB).
This innovation enhances sustainability in metal powder production by transforming otherwise unusable powders into high-quality AM materials.
Additionally, the P2P system can process elemental powders into homogeneous pre-alloyed materials. Trials with titanium and 10% molybdenum (Mo) elemental powders demonstrated its ability to produce custom alloys directly from base materials, eliminating the need for complex preprocessing.
Features and Advantages of the Powder2Powder System
-
Precision Control of Particle Size Distribution (PSD): Transforms oversized and irregular particles into AM-optimised powders.
-
Enhanced Powder Morphology: Plasma-based melting and ultrasonic atomisation refine particle shape, ensuring spherical, satellite-free particles.
-
Custom Alloy Production: Processes elemental powders or commercial alloys, eliminating preprocessing steps like electrode casting or wire drawing.
-
Multi-Material Compatibility: Supports steel, titanium, nickel, refractory alloys, and high-entropy alloys (HEAs) for varied AM applications.
-
Sustainability and Waste Reduction: Recycles metal powders, converting otherwise unusable materials into AM-ready feedstock, supporting sustainable manufacturing practices.
Transforming the AM Industry with Custom Powder Solutions
Amazemet’s Powder2Powder system is a game-changer for the Additive Manufacturing industry, addressing two key challenges:
-
Upcycling powder waste into usable AM material.
-
Producing custom alloy powders directly from base feedstock.
The P2P system enhances efficiency and sustainability in powder-based manufacturing, allowing manufacturers to create high-performance, customised powders for aerospace, automotive, and biomedical applications.
Attendees at Formnext 2024 will have the opportunity to witness the Powder2Powder system in action. Amazemet will showcase the system at Hall 12, E61, offering a comprehensive solution for metal powder recycling and custom alloy production.
Leave a Reply
You must be logged in to post a comment.