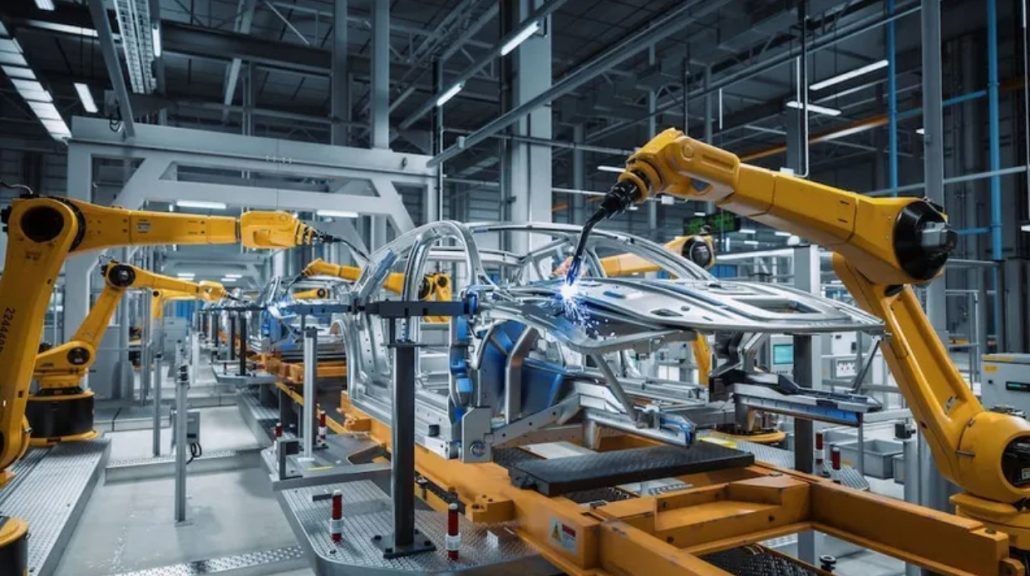
The metal industry is rapidly adopting automation and robotics to transform material handling processes. The focus is on minimizing manual handling and optimizing storage solutions. Companies are integrating cutting-edge technologies to boost efficiency, enhance safety, and improve inventory management in metal service centers.
Reducing Human Touchpoints for Greater Efficiency
Industry leaders emphasize that minimizing human interaction with materials is crucial for operational efficiency. Paul Short, president of Combilift North America, notes that fewer touchpoints translate to fewer errors and less damage. Companies like KASTO and Steel Storage Systems offer automated solutions integrated with warehouse management software. This enables real-time inventory tracking, efficient storage practices, and greater accuracy, ultimately preventing costly mistakes.
Automated systems with integrated scales provide instant inventory feedback, according to Stefan Dolipski, Vice President at KASTO. Every material movement is recorded, offering continuous inventory data. Lauren McCallin, COO at Steel Storage Systems, highlights the importance of optimized layout and accessibility for quick retrieval. Automated solutions now leverage historical data to predict material needs, preventing shortages and reducing manual labor.
Enhancing Safety and Addressing Labor Shortages
Automation and robotics are also addressing safety concerns and labor shortages. Automated guided vehicles (AGVs), automated storage and retrieval systems (ASRS), and overhead crane automation are gaining traction. These technologies increase productivity and minimize risks associated with manual handling, such as operator errors and collisions.
Safety is paramount in metal facilities, where manual handling often leads to injuries. Automation mitigates these risks. Kim Hindle, Chief Product Officer at CareGo Tek, explains that automation ensures safe and efficient product movement, eliminating the need for workers in hazardous environments. Sensors and AI technology further enhance safety by halting moving parts when operators enter restricted zones.
Labor shortages are driving further adoption of automation. Ron Piso from G.W. Becker Inc. observes that automated cranes, robots, and AGVs not only boost productivity but also create a safer, more appealing work environment, crucial in a sector facing labor challenges.
Leave a Reply
You must be logged in to post a comment.