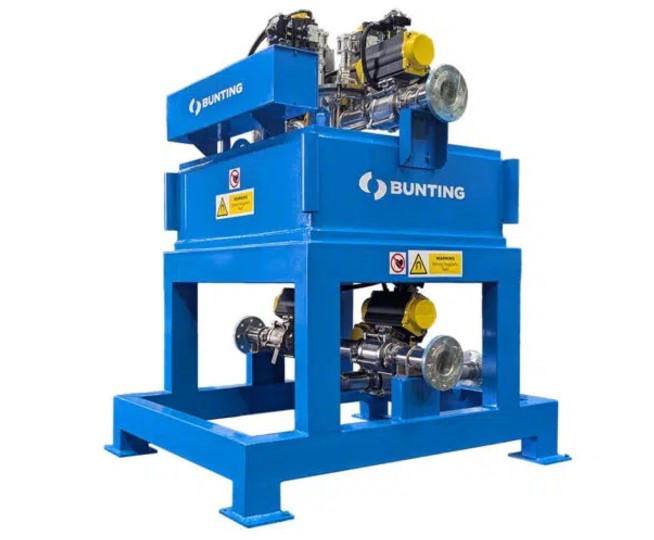
Bunting has launched a new Electromagnetic Wet Filter designed to tackle high-intensity magnetic separation challenges in liquids and slurries. The filter uses a magnetic field strength between 3,500 and 10,000 Gauss to separate fine iron particles and paramagnetic minerals. This innovation addresses the limitations of traditional magnetic separation technologies, which struggle with weakly magnetic particles.
Advanced Magnetic Technology for Multiple Industries
The Electromagnetic Wet Filter provides enhanced separation capabilities across various industries. In ceramics, it removes magnetic particles like free iron and paramagnetic minerals from slips and glazes, improving product quality. In mineral processing, it eliminates fine iron and minerals like hematite from non-metallic materials such as kaolin and silica sand. Additionally, it aids wastewater treatment in steel production and power plants by removing scale and free iron.
Enhanced Efficiency and Customizable Design
The filter’s high magnetic field gradient improves separation efficiency. It generates a much stronger localized magnetic field, up to three times the strength of the background field. This design ensures more effective removal of challenging magnetic particles, which is vital for industries requiring precision.
Streamlined Operation and Maintenance
The filter features automated cleaning systems and easy-to-maintain components, including a Siemens PLC and HMI interface. These ensure precise control over cleaning and operation, while the directional flushing mechanism helps remove captured magnetics, boosting performance for subsequent batches.
Cost and Time Efficiency for Industrial Applications
The Electromagnetic Wet Filter is energy-efficient due to oil-cooled electromagnetic coils that keep operating temperatures low. This reduces energy consumption. The filter also includes a built-in jig for safer, faster matrix handling, reducing maintenance time and increasing production uptime.
Solving Key Challenges in Wet Magnetic Separation
Adrian Coleman, Bunting’s European Technical Director, emphasized the filter’s ability to address high-intensity magnetic separation challenges. It reduces reject rates, minimizes rework costs in ceramics, and allows higher-quality processing in mineral processing without costly drying stages, enhancing operational cost efficiency.
Leave a Reply
You must be logged in to post a comment.