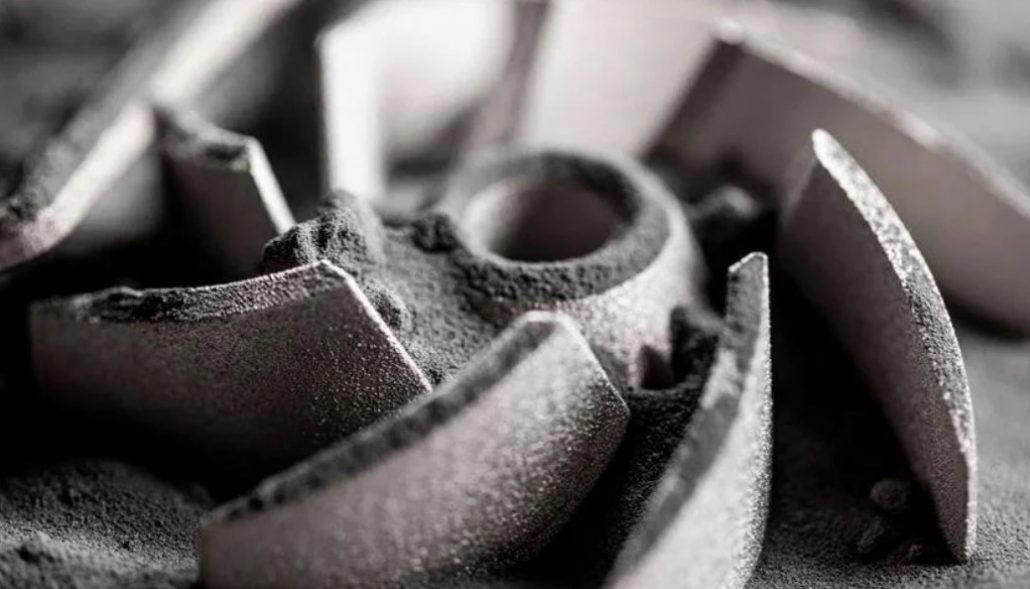
Innovative Metal Additive Manufacturing Technique to Enhance Aircraft Fleet Readiness
The Ohio State University’s Center for Design and Manufacturing Excellence (CDME) is collaborating on a cutting-edge project to demonstrate the potential of ColdMetalFusion (CMF) for producing replacement parts for aircraft. This technique, developed by Headmade Materials GmbH, is poised to enhance the speed, flexibility, and cost-effectiveness of the aircraft parts supply chain, offering significant improvements in both component performance and fleet readiness.
Michael Lander, CDME’s additive lead engineer, emphasizes the advantages of CMF: “We are looking to demonstrate that the use of this technique can significantly improve the speed, flexibility, cost, and performance of the component supply chain, enhancing the readiness and effectiveness of the U.S. Air Force.”
ColdMetalFusion: A Supportless Solution for Faster Production
ColdMetalFusion technique works by building parts layer-by-layer at lower temperatures compared to traditional metal additive processes. Unlike other techniques that require support structures to account for gravity and internal pressure, ColdMetalFusion allows parts to be built supportless, significantly speeding up repair times and reducing costs. This can be a game-changer for military applications, particularly in enhancing fleet sustainability and ensuring that critical aircraft parts can be produced on-demand.
The collaboration between CDME, Tinker Air Force Base’s Reverse Engineering and Critical Tooling (REACT) Lab, machine manufacturer EOS, industry partner Headmade Materials, and America Makes aims to assess the mechanical properties of the parts produced using the ColdMetalFusion technique.
First U.S. Academic Lab to Use ColdMetalFusion for Metal Parts
CDME is now the first academic laboratory in the United States to employ the ColdMetalFusion technique for producing metal parts. The lab is working to demonstrate that CMF is a viable solution for extending the lifespan of aircraft components, a critical need for the U.S. Air Force. By utilizing EOS’ P110 machine, traditionally used for polymer additive manufacturing, and Headmade Materials’ ColdMetalFusion feedstock, CDME is proving the versatility of this emerging technology for high-performance applications.
Kaleb Duarte, a CDME undergraduate research assistant, expressed his excitement about the project: “It’s a fascinating process. I’m excited to see how ColdMetalFusion makes metal 3D printing a more accessible and sustainable process across industries.”
Collaborative Effort with Key Industry Partners
The project brings together key stakeholders from academia, industry, and the military, with support from America Makes, the national accelerator for additive manufacturing. CDME’s research aims to provide evidence that ColdMetalFusion can be a reliable and scalable solution for the U.S. Air Force to produce durable, high-quality replacement parts for its aircraft fleet.
Leave a Reply
You must be logged in to post a comment.