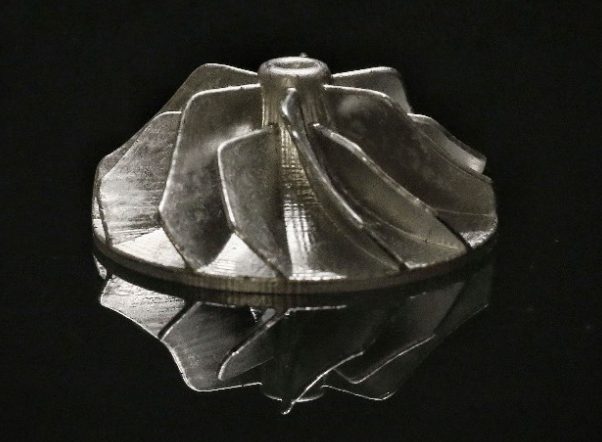
The ‘Simsalabim’ project aims to advance sinter-based Additive Manufacturing (AM) for nickel-based alloys. This collaborative initiative unites leading research institutions: Fraunhofer Institute for Manufacturing Technology and Advanced Materials (IFAM), Dresden University of Applied Sciences (HTW), and the Fraunhofer Institute for Material and Beam Technology (IWS). The project’s goal is to enhance sintering technologies for high-performance nickel-based superalloys, which are vital for high-temperature applications in industries like aerospace, energy, and hydrogen.
Boosting Efficiency and Accelerating Material Development
The Simsalabim project seeks to achieve Technology Readiness Level (TRL) 5, indicating readiness for industrial use. A key objective is to boost resource efficiency by cutting development cycles and accelerating material calibration. The team intends to shorten development timelines by two to three cycles and speed up calibration by five times. Additionally, the initiative will develop sintering processes and new materials, providing industrial partners with more options for high-performance components. The project plans to establish a regional network for sinter-based AM, with potential future expansion to include materials like tool steels and cobalt-based alloys.
Sinter-Based AM: A Solution for Challenging Materials
Traditional metal AM has largely relied on laser-based processes, which, while mature, struggle with challenging materials and complex geometries. This has sparked growing interest in sinter-based Additive Manufacturing (AM). Sinter-based AM offers advantages such as material versatility, cost-effectiveness, and high productivity. Unlike fully melting metal powders, sintering processes use powders that do not completely melt. This method reduces issues like thermal gradients, residual stresses, and cracking. It is ideal for hard-to-weld materials such as nickel-based superalloys.
Nickel-based alloys are prized for their high strength, corrosion resistance, and thermal stability. These properties make them crucial for sectors like aerospace, energy, and hydrogen. However, processing these materials with laser-based methods is challenging, especially in terms of preventing cracks and maintaining material integrity. Sinter-based AM addresses these issues by ensuring the production of high-quality, crack-free components.
Overcoming Challenges and Enhancing Material Properties
Despite its potential, sinter-based AM remains less mature than laser-based methods, especially in terms of precision and material properties. One significant challenge involves predicting and compensating for sintering shrinkage in complex structures. Achieving high strength, fatigue resistance, and a good surface finish is also essential. The Simsalabim project focuses on improving material properties by developing more accurate simulations for predicting sintering behavior. These advancements will help achieve better control over final part quality. The initiative aims to refine sintering and post-processing techniques to enhance the material properties of nickel-based superalloys for high-temperature applications.
Collaboration Driving Innovation
To ensure that the project aligns with industry needs, manufacturers and users of high-temperature materials are invited to a network meeting on November 27-28, 2024. This event will allow experts to provide input, ensuring that the solutions being developed are both practical and scalable. The Fraunhofer research teams, along with Dresden University of Applied Sciences, will leverage their expertise in additive manufacturing, powder metallurgy, and high-performance materials to drive the project forward.
Leave a Reply
You must be logged in to post a comment.