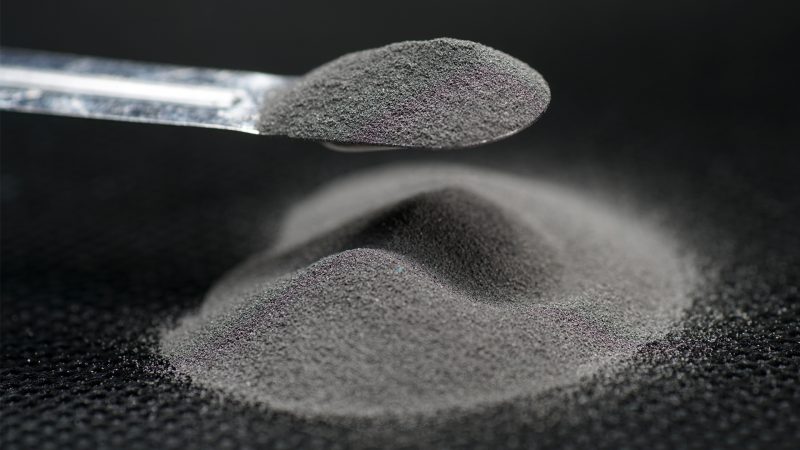
Continuum Powders, a California-based company, is revolutionizing the metal powder industry by transforming metal scrap into high-quality powders for Additive Manufacturing (AM). Their process reclaims used metal parts and converts them into premium, ASTM-certified powders, offering a sustainable and cost-effective alternative to traditional metal powder production. This approach reduces waste while providing a reliable material source for advanced manufacturing.
Sustainability at the Core of Metal Powder Production
The traditional metal powder industry is heavily reliant on virgin material extraction, which leads to habitat destruction, carbon emissions, and volatile raw material prices. Continuum Powders addresses these challenges with a circular economy approach, reducing the need for new material extraction and minimizing environmental impact. By converting scrap metal into powder, the company helps lower energy consumption and carbon footprints.
The Scrap-to-Powder Process: A Detailed Overview
Continuum Powders employs a multi-step process to convert scrap metal into premium powder suitable for AM applications:
-
Collection and Sorting: Scrap metal is carefully sorted by material type and alloy composition to ensure quality.
-
Cleaning and Preprocessing: Scrap is cleaned to remove impurities, ensuring a contaminant-free powder.
-
Size Reduction: The metal is reduced to smaller pieces, preparing it for atomisation.
-
Atomisation: The metal is melted and atomised into fine, spherical powder particles using gas or water.
-
Quality Control: The atomised powder undergoes rigorous quality tests to meet ASTM standards for industries such as aerospace and automotive.
Advanced Greyhound M2P Technology: Transforming the Industry
The proprietary Greyhound Melt-to-Powder (M2P) technology is a key innovation at Continuum Powders. In particular, this technology directly converts reclaimed metal scrap into high-quality powder. Furthermore, it optimizes particle size, shape, and flowability for various AM processes, including Laser Beam Powder Bed Fusion (PBF-LB) and Electron Beam Powder Bed Fusion (PBF-EB). Additionally, the process reduces energy consumption and waste, thereby creating a more sustainable supply chain.
Advantages of Using Reclaimed Metal Powders
-
Environmental Benefits: Reducing the need for virgin material extraction helps minimize environmental impact and supports a circular economy.
-
Cost-Effective Solution: Reclaimed powders are more affordable than virgin powders, offering manufacturers a cost-effective option for AM.
-
Consistency and Quality: Rigorous quality control ensures that reclaimed powders match or exceed the performance of virgin powders.
-
Stable Supply Chain: Reclaimed powders provide a stable, predictable supply, mitigating risks associated with volatile raw material prices.
A Sustainable Future for Metal Powder Manufacturing
Continuum Powders is leading the way in creating a more sustainable metal powder industry. By recycling scrap metal into ASTM-grade powders, the company reduces waste, lowers costs, and supports a circular economy. As the demand for metal powders in Additive Manufacturing grows, Continuum Powders offers a reliable and eco-friendly material solution for manufacturers.
Leave a Reply
You must be logged in to post a comment.