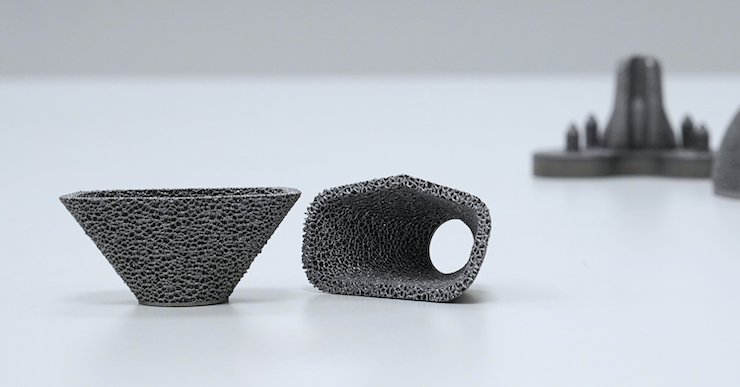
Croom Medical has partnered with Global Advanced Metals (GAM) to create a closed-loop supply chain for tantalum powder, revolutionizing the production of 3D printed medical implants. This new system promises to improve sustainability, reduce costs, and streamline production, pushing the boundaries of what’s possible in medical device manufacturing.
Pioneering Sustainability with Tantalum Powder
Tantalum, known for its strength and biocompatibility, is commonly used in aerospace and electronics. However, the metal has proven increasingly valuable in the medical field, particularly for implants like dental replacements and joint prosthetics. Despite its advantages, using tantalum in industrial 3D printing has been challenging due to material waste and inefficient recycling methods.
Croom Medical and GAM have recognized the untapped potential of tantalum in additive manufacturing. By developing a closed-loop supply chain, the companies aim to address key challenges like material waste and cost inefficiency. This system involves recycling used tantalum powder and reusing it in the production cycle, ensuring sustainable and cost-effective manufacturing processes.
The Process: Efficient Recycling and Reuse
The closed-loop system begins when Croom Medical uses tantalum powder in 3D printing medical implants. After printing, any unused or end-of-life powder is sent to GAM for recycling. GAM reprocesses the powder, returning it to Croom for reuse in future production. This continuous cycle minimizes material waste, reduces the need for new raw materials, and lowers overall costs.
Croom Medical employs Colibrium Additive’s M2 laser powder bed fusion system, a technology designed for high-precision 3D printing. This system enables the creation of complex, customized, and osteoconductive structures tailored to individual patients. Croom’s advanced techniques have allowed the company to manufacture over 60,000 medical devices, demonstrating its expertise in additive manufacturing.
Delivering Sustainable Medical Solutions
The new closed-loop system is now available under Croom Medical’s contract manufacturing model, with multiple customers already in the prototyping phase. This partnership allows Croom to offer a reliable, efficient, and sustainable solution for 3D printed tantalum medical devices. By reusing tantalum powder, the companies are reducing environmental impact while improving the efficiency of medical device production.
Dr. Shane Keaveney, R&D Manager at Croom Medical, emphasized the benefits: “Tantalum’s unique properties make it perfect for next-generation implants. Through our collaboration with GAM, we provide tailored solutions that meet the specific needs of our OEM customers.”
As more companies adopt this closed-loop approach, the medical device industry could see significant advancements in both sustainability and efficiency. By integrating cutting-edge technology with sustainable practices, Croom Medical and GAM are setting a new standard for 3D printed medical implants.
Leave a Reply
You must be logged in to post a comment.