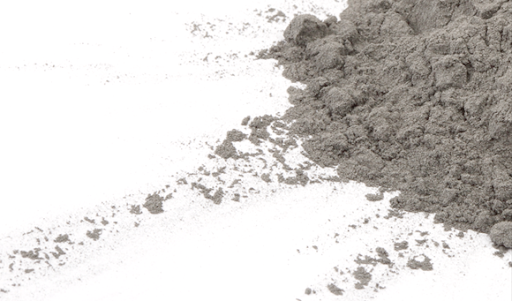
Kyhe Technology (Ningbo) Co Ltd, a leader in the titanium alloy industry based in Ningbo, China, introduces a more sustainable approach to titanium alloy powder production. Utilizing its innovative DH-S technology (Dehydrogenation Spheroidal), Kyhe Tech offers a cost-effective and environmentally friendly alternative to traditional methods. This technology enables the use of recycled titanium materials, reducing reliance on virgin resources and significantly lowering production costs. Kyhe Tech targets industries such as aerospace, automotive, consumer electronics, and renewable energy. These industries require high-performance, durable materials for advanced applications.
Sustainability Integrated into Operations
Kyhe Tech’s operations prioritize sustainability and responsible manufacturing. Its 9,800 m2 facility holds Environmental, Social, and Governance (ESG) certification. This reflects its commitment to eco-friendly practices. Additionally, the company holds the Global Recycled Standard (GRS) certification. This ensures its processes meet global standards for recycling and environmental responsibility. By focusing on recycled titanium and minimizing energy-intensive processes, Kyhe Tech reduces greenhouse gas emissions and waste generation. This makes its products more sustainable than traditional methods.
DH-S Technology: Cost-Effective and High-Performance Powders
The DH-S technology developed by Kyhe Tech advances titanium alloy powder production. Unlike atomization methods like EIGA, which require high energy and virgin titanium, DH-S uses recycled raw materials. These include titanium alloy scrap, CNC machining chips, and sponge titanium fragments. This ability to use recycled materials reduces production costs by up to 60% compared to EIGA. The use of recycled titanium makes the process cost-efficient. It also supports the global transition to sustainable manufacturing practices.
High-Quality Powders for Demanding Applications
The titanium powders produced by DH-S technology meet high mechanical standards. These standards are required in aerospace, automotive, and medical industries. The powders exhibit high tensile strength and fatigue resistance. This makes them suitable for demanding applications. These include Additive Manufacturing, Metal Injection Moulding, and coating processes. The DH-S process achieves a 95% single-batch yield rate. This minimizes material waste and maximizes production efficiency. This efficiency, combined with high-quality mechanical properties, offers manufacturers premium materials at a reduced cost.
Revolutionizing Titanium Alloy Production with Sustainability
Kyhe Tech’s DH-S technology transforms the titanium alloy powder industry. It combines cost-efficiency, sustainability, and high-performance materials. The company’s commitment to responsible manufacturing reduces waste and emissions. This makes it a leader in greener manufacturing. With advanced recycling and innovative technology, Kyhe Tech supplies industries with affordable, environmentally friendly titanium alloys. SuperMetalPrice notes that the development of sustainable and cost-effective titanium production methods, such as Kyhe Tech’s DH-S technology, is crucial for expanding the use of titanium alloys in various industries. This expansion can influence the demand and supply dynamics of titanium and its related materials.
Leave a Reply
You must be logged in to post a comment.