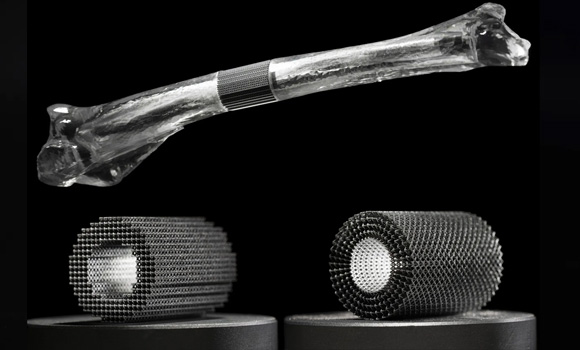
Researchers at RWTH Aachen University in Germany are pioneering the use of Additive Manufacturing (AM) to create patient-specific bioresorbable implants. These implants, made from zinc-magnesium alloys, aim to address critical size bone defects, such as those in long bones, with fewer side effects. This breakthrough collaboration is part of the reACT (Resorbable Solutions from the Aachen Technology Region) alliance.
Additive Manufacturing: A Game-Changer for Bioresorbable Implants
When bone defects are caused by accidents, congenital malformations, or tumor resections, they often require complex and expensive reconstructive procedures. Traditional implants, like titanium, may increase fracture risks due to stress shielding and often need follow-up surgeries. This has driven the need for innovative materials and design methods to improve clinical and socio-economic outcomes.
Through Additive Manufacturing, the reACT alliance is developing patient-specific implants tailored to the exact shape of a bone defect. The new algorithm-based design configurator automatically generates optimized implant designs based on critical factors like bone density, defect geometry, age, and weight.
Automated Patient-Specific Implant Design
The algorithm-based design configurator integrates geometric, logical, and mathematical operations to create an implant design that meets specific functional requirements. This method is adaptable to other medical applications, such as spinal cages and maxillofacial implants. Initially, CT scan data of the defect site determines the geometry, followed by adaptive lattice structures within the design. These lattice structures promote new tissue growth and encourage the efficient removal of degradation products.
Material Innovation for Bioresorbable Implants
Zinc and magnesium alloys have shown great promise for resorbable bone implants. Zinc offers favorable degradation properties but lacks sufficient mechanical strength for implants. Magnesium, widely used in orthopaedic implants, provides better mechanical properties but has issues with rapid degradation and gas formation in moist tissue environments. Extensive alloy screening has led to the discovery of the ideal ZnMg alloy composition (≤1 wt% magnesium), which balances strength and resorbability.
First Demonstrator and Future Applications
The reACT alliance has already produced the first demonstrator implant using Additive Manufacturing. The implant design is customized to fit the patient’s bone structure, and the generated lattice structures can be adjusted for optimal healing and resorption. The flexibility of this method ensures that the implant adapts to the patient’s biomechanical needs, minimizing refracture risks.
Key Project Partners in the reACT Alliance
The reACT alliance includes several notable institutions and companies:
-
Meotec GmbH
-
Medical Magnesium GmbH
-
Fibrothelium GmbH
-
University Hospital Aachen
-
Fraunhofer Institute for Laser Technology (ILT)
-
RWTH Aachen – Chair Digital Additive Production (DAP)
The alliance is part of the RUBIN program, funded by the German Federal Ministry of Education and Research (BMBF).
Leave a Reply
You must be logged in to post a comment.