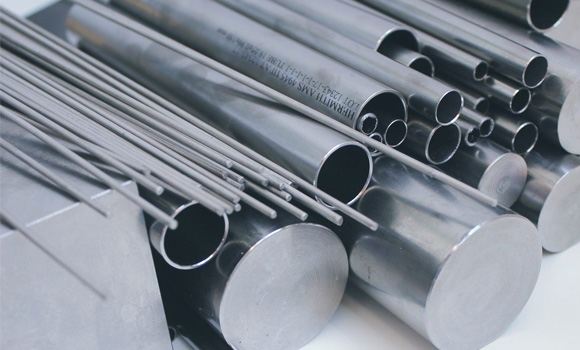
Hermith GmbH, a leading titanium supplier based in Munich, Germany, has developed an improved method for producing titanium Ti-6Al-4V wire. This process, tailored for Additive Manufacturing (AM), is vital for industries such as aerospace, medical, and automotive. Ti-6Al-4V alloys are known for their strength, corrosion resistance, and durability. Hermith’s new method improves both material quality and manufacturing efficiency.
Challenges in Titanium Wire Manufacturing
Titanium wire production for Additive Manufacturing involves multiple stages: heating, deformation, and annealing. Traditional methods to create high-strength Ti-6Al-4V wire often require energy-intensive processes, like etching and vacuum annealing. These steps can lead to oxidation, surface cracking, and structural inconsistencies, affecting the wire’s mechanical properties. Additionally, conventional methods result in longer processing times and lower mechanical performance compared to more advanced approaches.
Hermith’s Solution for Titanium Wire Production
Hermith’s improved method uses induction heating combined with precise process control. This technique minimizes anisotropy in the mechanical properties and ensures that the wire is a continuous piece without welded joints. The wire is produced in lengths of at least 8,500 meters, making it ideal for Additive Manufacturing applications that demand high consistency and reliability.
The process begins by heating the billets. For billets sized 8.0 mm to 4.0 mm, induction power of 50–70 kW at 40–80 kHz is applied. For smaller billets (under 4.0 mm), induction power ranges from 20–40 kW at 300–500 kHz. The billets are heated to temperatures between 400–700°C during drawing or rolling, with careful control to ensure high-quality wire.
Hermith’s method ensures uniform temperature distribution along the wire. This minimizes scale formation and contamination during heat treatment. Acoustic emission parameters are used to control deformation, reducing rolling passes while maintaining strength and plasticity.
Key Findings and Benefits
Hermith’s method has significantly improved Ti-6Al-4V wire compared to traditional methods. The produced wire has a fine-grained structure and uniform grain distribution. Mechanical properties, such as a plasticity parameter above 3.2 mm, show minimal anisotropy. These improvements make the wire ideal for Additive Manufacturing, meeting the strict requirements of aerospace, medical, and automotive industries.
However, the process remains economically challenging. The low deformation rate extends production time, potentially impacting cost-efficiency. Further optimization may be needed to improve the economic viability of the process.
Conclusion: Advancing Titanium Wire in Additive Manufacturing
Hermith’s improved titanium wire manufacturing process represents a significant step forward in Additive Manufacturing. The company’s use of induction heating and advanced process control enhances Ti-6Al-4V wire quality, reducing defects and improving mechanical properties. This breakthrough strengthens the potential of titanium alloys in high-performance industries, paving the way for future innovations in Additive Manufacturing.
Leave a Reply
You must be logged in to post a comment.