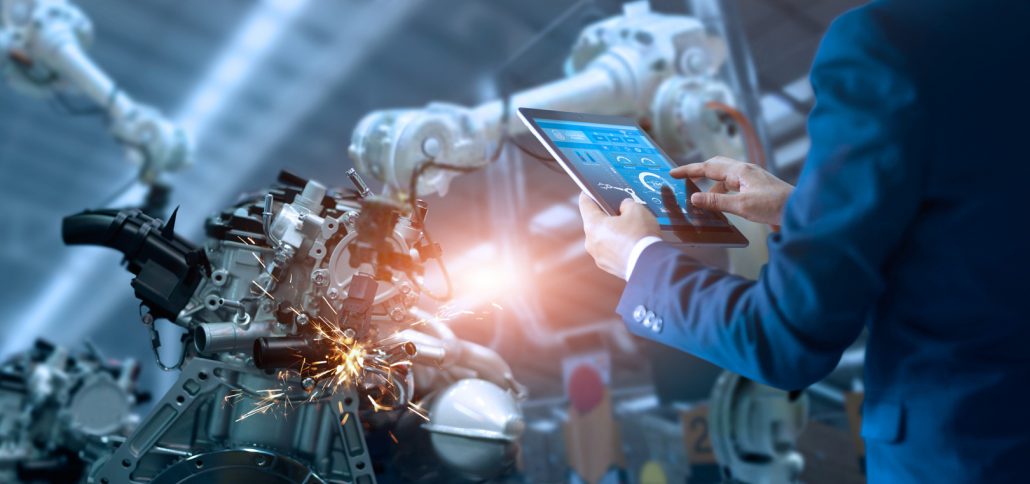
Smart manufacturing is transforming business operations in 2025. While offering significant potential, it also presents challenges, especially for smaller suppliers. These challenges include defining what smart manufacturing means for their specific operations, determining which processes to apply it to, and finding the right workforce to manage new technologies. Small manufacturers must also anticipate infrastructure needs for integrating these innovations.
Despite these hurdles, successful implementation of smart manufacturing can yield better efficiency, improved product quality, and enhanced sustainability across the supply chain. Companies can overcome these challenges by working together to establish clear industry standards, develop their workforce, and ensure data integrity throughout the manufacturing process.
Key Areas for Manufacturers to Focus On
1. Universal Industry Standards for Material Testing
Reliable material testing is crucial for successful smart manufacturing adoption. Establishing universal testing standards helps manufacturers make informed decisions. Inconsistent testing can lead to unreliable simulations and improper tooling, compromising production.
Maintaining well-calibrated equipment and providing thorough training for testing operators is essential. Adopting universal standards for testing can reduce confusion and increase the reliability of material properties across the industry.
2. Workforce Development and Skills Training
Workforce development is critical due to rapid advancements in automation, new materials, and testing technologies. Fabricating professionals need to stay ahead of the curve. Companies should invest in training their workers to troubleshoot problems, understand new processes, and adapt to smart manufacturing demands.
Smart manufacturing will likely reduce the need for low-skilled labor but increase demand for highly skilled workers. These workers can manage complex systems, maintain new technologies, and support data-driven decisions. Developing a strong workforce ensures companies can continue to innovate and operate efficiently.
3. Controls to Ensure Data Integrity and Technological Accuracy
Ensuring data integrity is crucial as manufacturers adopt technologies like AI and data analytics. While data analysts are important, smart manufacturing is not a substitute for human judgment. Technology alone cannot guarantee success.
Manufacturers must train employees to manage data accuracy, ensure system integrity, and maintain monitoring devices. This helps prevent errors, mitigate risks, and protect company values and operational goals.
Leave a Reply
You must be logged in to post a comment.