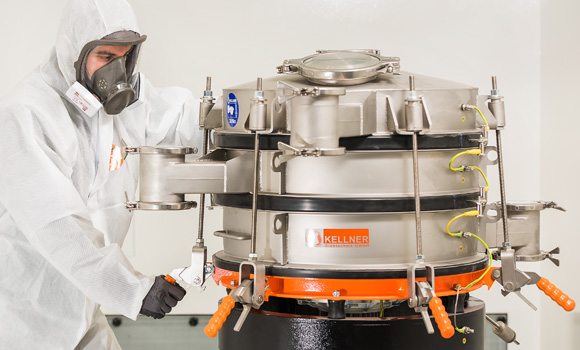
Renishaw, based in Wotton-under-Edge, Gloucestershire, UK, has partnered with Metalpine, from Graz, Austria, to develop copper-nickel (CuNi) alloy powders. These powders are designed for marine environments where naval components face extreme challenges like saltwater corrosion and moisture exposure.
The Importance of Copper-Nickel Alloys in Marine Environments
Naval operations in saltwater environments pose significant challenges. Hydraulic components and other parts quickly wear and corrode. To address this, a European naval force decided to manufacture in-house replacement parts. Using Renishaw’s RenAM 500Q Flex Additive Manufacturing (AM) machine, they can produce durable parts quickly, reducing reliance on lengthy supply chains.
CuNi alloys like CuNi 10 (10% nickel, 90% copper) and CuNi 30 (30% nickel, 70% copper) form a protective layer on parts, preventing degradation. This makes them ideal for harsh marine conditions. Renishaw and Metalpine engineers have developed optimized process parameters to manufacture these alloys effectively.
Advanced Manufacturing and the Development of CuNi Alloys
Copper-based alloys like CuNi 10 are challenging for additive manufacturing. CuNi 10 is highly reflective, which resists laser energy. In contrast, CuNi 30 is easier to process due to its higher nickel content.
Renishaw’s advanced laser melting technology and the RenAM 500Q Flex machine have overcome these challenges. The team conducted extensive testing to refine parameters like laser power, scan speed, and hatch distance. These efforts have enabled the production of high-quality, durable parts for marine applications.
Efficient Powder Manufacturing for Marine Parts
Metalpine is known for its expertise in producing high-quality metal powders. Their process ensures high sphericity and porosity-free particles. These qualities are essential for meeting the rigorous demands of naval operations. Gerald Pöllmann, CEO of Metalpine, praised Renishaw’s AM engineers. Their collaboration led to the creation of tailored powders that meet the naval forces’ specifications.
The RenAM 500Q Flex’s open-loop powder system allows for quick powder swapping. This feature makes it ideal for optimizing material properties and part designs. With the Reduced Build Volume (RBV) accessory, material testing can be done with as little as 0.25 liters of powder.
Optimizing Manufacturing for Durable Marine Components
With refined settings and optimized laser processing parameters, Renishaw and Metalpine overcame the challenges of copper-nickel alloys in additive manufacturing. The result is durable parts that perform well in extreme marine conditions. This ensures that naval components can withstand constant exposure to saltwater and environmental stress.
The collaboration highlights the potential of additive manufacturing for creating high-quality, customized parts. Renishaw and Metalpine’s work paves the way for more efficient and sustainable solutions in the defense and marine industries.
Leave a Reply
You must be logged in to post a comment.