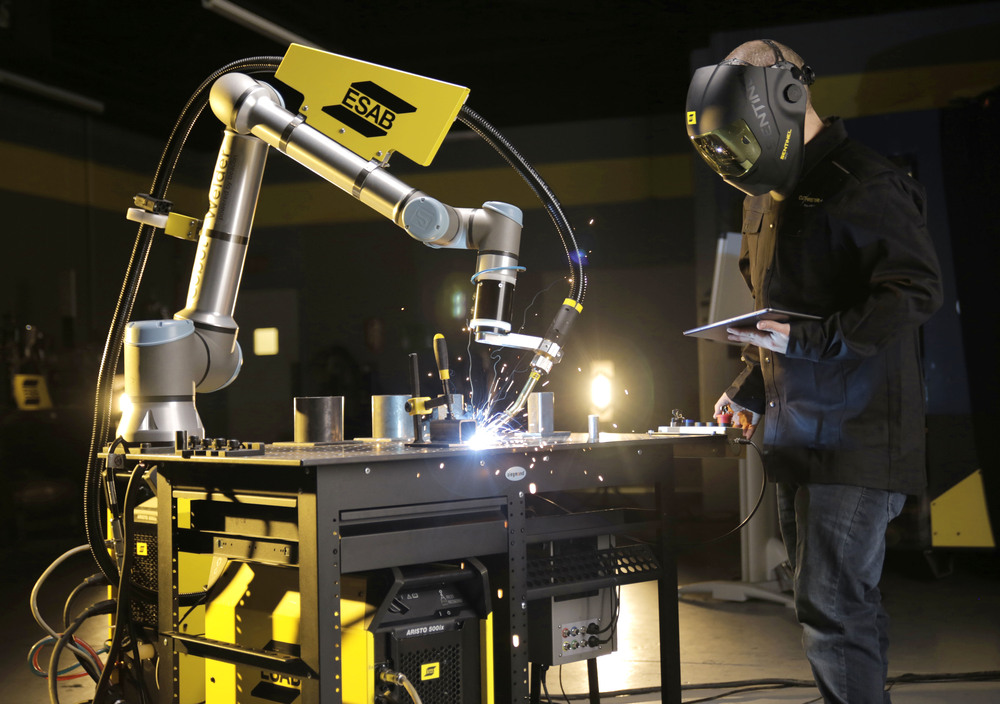
Collaborative robot-based welding systems (cobots) have undergone rapid advancements, providing innovative solutions for industries traditionally relying on manual welding. These cobots not only enhance welding quality but also significantly increase productivity and worker safety. Today’s cobots have moved beyond simple, fixed-location tasks to tackle more complex welds in a wide range of industries.
The Rise of High-Performance Welding Cobots
The evolution of welding cobots has shifted from simple tasks to high-performance applications. Initially, cobots were designed for basic, low-complexity welding tasks mounted on fixed tables. However, recent developments have introduced more sophisticated capabilities, such as external axis positioners and coordinated motion systems. These advancements allow cobots to take on high-mix, low-volume and high-volume production with equal ease.
The benefits are clear. Cobots extend arc time per shift, accelerate part setup and changeovers, and streamline production processes. By enhancing process repeatability, they ensure greater consistency in weld quality while reducing rework. This improved efficiency is especially impactful in industries with high labor turnover. Cobots take on the most repetitive, dangerous, and physically demanding tasks, allowing workers to focus on more specialized, creative, and high-value tasks.
Portability Opens New Opportunities Across Industries
One of the most significant advantages of modern welding cobots is their portability. This feature allows them to be brought to the weld, rather than moving heavy, bulky parts to a fixed robotic system. This shift in approach opens doors for automation in industries such as shipbuilding, construction, and manufacturing. These are sectors where traditional automated systems had limitations due to space constraints or the size of workpieces.
The lightweight design and small form factor of welding cobots allow them to be easily moved across the workspace. In industries like shipbuilding, this mobility enables cobots to perform welds on massive, curved surfaces. Previously, manual welding was the only option for such surfaces. For instance, a Canadian manufacturer of earth-moving equipment introduced a custom skid. This allowed their welding cobot to work on 15-ton truck bodies. The result is a significant increase in output. The cobot assists in welding fillet joints on large, complex components.
Cobots can also be mounted on movable magnetic rails, providing the ability to “crawl” along flat or curved surfaces to perform welds. This capability not only allows fabricators to save valuable time but also makes automated welding possible in applications traditionally reserved for manual labor. This new form of portable welding automation has proved especially beneficial for smaller fabricators. These fabricators previously lacked access to expensive traditional robotic systems.
Increasing Adoption of Cobots in Challenging Environments
Cobots have also found their place in industries requiring work in tight, hard-to-reach areas. Shipbuilding, for example, often involves welding inside narrow rooms and cubicles in ships. This job is typically performed manually due to limited space. With their portability, cobots are now able to work in these challenging environments, reducing the physical strain on workers.
In construction and manufacturing, the ability to bring the cobot to the job site has led to increased efficiency. A Swedish bucket repair company, for instance, found that using a portable welding cobot cut their working time by 30%. This enabled them to take on more complex welding tasks.
Choosing the Right Cobot: Factors to Consider
When selecting a welding cobot, usability is crucial. A skilled welder should be able to program simple welding tasks within a day. Therefore, it is important to choose a cobot with an intuitive interface and accessible training resources. Companies that offer online training and certification can help fabricators get up to speed quickly. This ensures seamless integration into their operations.
It’s also essential to select a proven cobot from a reputable manufacturer. A trusted supplier will offer welding-specific tools and programming support. This ensures the cobot meets the needs of a variety of welding applications.
Conclusion
Welding cobots have transformed the automation landscape, offering a combination of flexibility, portability, and ease of use that traditional robots couldn’t match. By increasing productivity, enhancing weld quality, and reducing worker strain, these robots are redefining how welding tasks are completed. With continued advancements in cobot technology, industries of all sizes can benefit from more efficient, cost-effective, and safe welding solutions.
Leave a Reply
You must be logged in to post a comment.