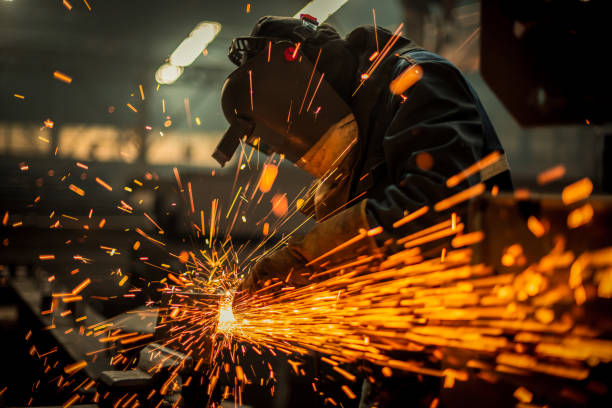
Market Trends and Price Pressures
As fabricators look toward 2025, several market dynamics will shape their strategies. A post-pandemic rebound in durable goods sectors like automotive and home appliances is expected to continue. Vehicle sales, while modest, will show steady growth, and demand for home appliances will follow suit. However, fabricators must brace for increasing price pressures, especially in the automotive sector. Consumer expectations for lower prices, combined with rapidly evolving vehicle features, will force manufacturers to find innovative ways to cut costs. A recent survey showed that consumers are willing to pay $35,000 for a new car, yet the average transaction price has risen to nearly $48,000. This price gap will create challenges for suppliers and fabricators, who must adapt their processes to meet new pricing and feature demands.
Pressure for Innovation and New Materials
As product features and consumer preferences continue to evolve rapidly, manufacturers must stay flexible to accommodate new materials and production processes. The rising demand for electric vehicles (EVs) will be a significant driver of this change, with battery electric vehicles (BEVs) expected to slowly increase market share. This shift, combined with the automotive industry’s focus on lightweighting and safety, will require the widespread adoption of new materials. Fabricators will need to develop the capability to handle advanced materials that are not only lightweight but also provide the necessary strength and durability for vehicles and other critical applications. With major manufacturers like Tesla facing market share losses, more traditional and emerging players are likely to ramp up their EV offerings and innovations, increasing the demand for fabrication services and materials.
Technological Advancements Shaping Fabrication Processes
Technological advancements will play a crucial role in the fabrication industry’s adaptation to the market changes anticipated in 2025. Automation is at the forefront, as robots and machines increasingly collaborate with human workers to boost efficiency, quality, and precision. Robotics and smart manufacturing technologies will allow fabricators to collect and analyze data through IoT devices, enhancing maintenance planning, production scheduling, and overall process optimization. These innovations help manufacturers stay competitive by reducing waste, improving throughput, and ensuring superior quality control. Machine learning will also contribute to optimizing designs and processes, offering faster iterations in product development, identifying constraints earlier, and enhancing decision-making processes. Together, these technologies will enable fabricators to meet the increasing demands for speed, precision, and cost-effectiveness.
The Role of Research and Workforce Adaptation
As the global competition for research and technological innovation intensifies, fabricators must also adapt by investing in research to enhance materials, tooling, and manufacturing techniques. The U.S. faces growing challenges in technological leadership, particularly as sentiments shift against science and technology. To maintain a competitive edge, fabricators must support initiatives in research and development, especially in materials science and process optimization. At the same time, the workforce will need to evolve. As automation and machine learning become more integrated into production lines, ensuring that employees are well-trained in new technologies will be key to success. Both labor and management must collaborate to develop effective training programs that promote safe, efficient, and productive work environments.
Sustainability and Efficiency in Manufacturing
Sustainability will remain a driving force for the fabrication industry, particularly in response to growing environmental concerns and regulatory pressures. In 2025, fabricators will be expected to implement sustainable practices, from reducing energy consumption to minimizing waste and using more recycled materials. At the same time, the push for efficiency will require fabricators to continuously improve their production processes, integrating new technologies that help reduce energy consumption and waste. Smart manufacturing solutions, including the use of predictive maintenance and process optimization tools, will help ensure that manufacturing remains not only cost-effective but also environmentally responsible.
Leave a Reply
You must be logged in to post a comment.