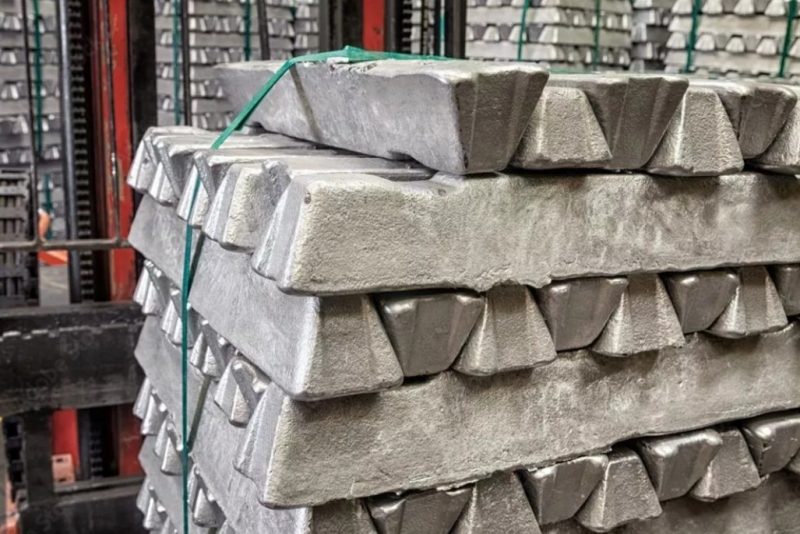
Aluminum is becoming the material of choice in industries like automotive and construction. Its lightweight, durability, and corrosion resistance make it essential for these sectors. As global demand for aluminum rises, the use of recycled aluminum (secondary aluminum) is also increasing. While secondary aluminum is energy-efficient, it faces challenges in corrosion resistance. New surface treatment technologies are addressing these issues, improving aluminum’s durability and lifespan.
Aluminum’s Rising Demand in Automotive and Construction Industries
Aluminum is ideal for electric vehicles (EVs) because of its lightweight properties. Reducing weight improves battery efficiency and range. On average, EVs use 30% more aluminum than traditional vehicles. This includes aluminum in battery enclosures, body structures, and lightweight components. The growing reliance on aluminum aligns with global efforts for sustainable and energy-efficient transportation.
In construction, aluminum is crucial for windows, facades, doors, and structural elements. It reduces overall building weight and improves energy efficiency. As sustainability regulations tighten, aluminum’s role in energy-efficient construction continues to grow.
The Shift Towards Secondary Aluminum
The rising demand for aluminum in automotive and construction sectors has increased the use of recycled aluminum. Secondary aluminum offers environmental benefits, reduces manufacturing costs, and saves energy during production. However, impurities and variations in alloy composition can affect corrosion resistance, limiting its use in high-performance applications.
Innovative surface treatment technologies address these concerns. Anodizing, trivalent chromium passivation, and optimized conversion coatings significantly improve corrosion resistance. These advancements make secondary aluminum a viable alternative for high-performance applications.
Advanced Corrosion Protection for Secondary Aluminum
Secondary aluminum alloys, especially in EV battery enclosures and construction, are prone to corrosion. Uniform corrosion degrades the entire surface, while filiform corrosion damages the protective coating. Both forms of corrosion reduce material longevity.
Several advanced surface protection methods are improving aluminum’s durability:
- Trivalent Chromium Passivation (TCP): This creates a robust protective layer, offering superior corrosion resistance in harsh environments.
- Anodizing: Converts the natural oxide film into a thicker layer, improving surface hardness, chemical resistance, and durability.
- Chromium-Free Coatings (Cr-Free): These eco-friendly coatings protect against environmental degradation and filiform corrosion, especially under painted surfaces.
- Hybrid Coating Systems: Combining anodizing with sealants or organic coatings enhances protection, especially in extreme conditions.
These technologies are vital for EV manufacturing, where material stability and long-term performance are crucial. With these solutions, secondary aluminum meets the rigorous demands of automotive and construction industries.
Enhancing Corrosion Resistance in EN AC 46000 for EV Battery Enclosures
A recent study on EN AC 46000, an aluminum alloy used in EV battery enclosures, highlighted the impact of copper on corrosion resistance. While copper enhances mechanical properties, it reduces corrosion resistance.
Untreated EN AC 46000 failed after eight hours in a neutral salt spray (NSS) test. However, using Iridite TCP III passivation improved corrosion resistance, extending NSS performance to 120 hours. Postdip treatments, such as Iridite Cor-Guard 40, increased surface hydrophobicity and significantly improved corrosion resistance. Treated samples maintained protection for up to 480 hours in harsh testing conditions.
Looking Ahead: The Future of Recycled Aluminum
As aluminum demand grows globally, secondary aluminum will play a critical role in sustainable manufacturing. Advancements in corrosion protection technologies have made secondary aluminum a viable solution for high-performance applications. These innovations help industries meet environmental goals while maintaining performance standards.
Emerging technologies like nanocoatings and self-healing layers have the potential to further enhance recycled aluminum’s durability. Collaboration between material scientists, manufacturers, and regulatory bodies will be essential to establish standards that maximize aluminum’s sustainability and performance.
Leave a Reply
You must be logged in to post a comment.