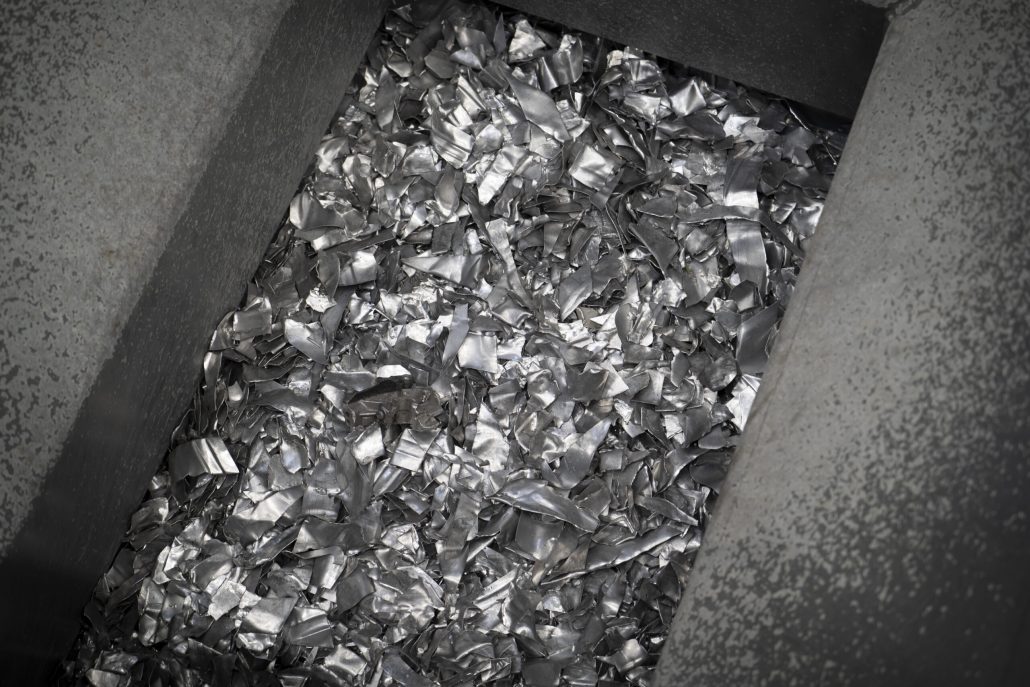
Revolutionizing Aluminum Recycling with LIBS Technology
Laser-Induced Breakdown Spectroscopy (LIBS) technology is transforming aluminum recycling. This breakthrough enhances the efficiency and sustainability of recycling processes. Constellium SE, a leading aluminum manufacturer, has teamed up with a German automaker and OSR GmbH & Co. KG, a recycling company, to improve aluminum recycling from automotive production. Their partnership tackles the challenge of sorting mixed aluminum scrap, particularly from the 5000 and 6000 alloy families. In the past, these materials were downcycled due to difficulties in sorting. With LIBS, they now sort the scrap with over 95% purity, making it suitable for high-quality aluminum products, especially in the automotive sector.
LIBS Technology Unlocks the Potential of Mixed Scrap
LIBS technology revolutionizes aluminum recycling by sorting scrap by alloy family quickly and accurately. Fanny Mas, a metallurgist at Constellium, explained that automotive production often generates mixed aluminum scrap, which is difficult to reuse directly. Before LIBS, processors shredded the scrap and used magnets to remove ferrous contamination, but the material still needed extensive processing. LIBS sorts the aluminum into pure alloy streams, like the 5000 and 6000 series, making it easier to remelt and reuse in new products. This process significantly boosts both the efficiency and sustainability of aluminum recycling.
Achieving Closed-Loop Recycling for Automotive Products
This partnership allows Constellium to manufacture aluminum products with high scrap content without compromising material integrity. Automotive scrap, which would traditionally be downcycled, can now be recycled back into automotive components. Since 2023, Constellium has melted tons of LIBS-sorted scrap at its Neuf-Brisach plant in France, reducing its reliance on primary aluminum. By using preconsumer scrap, Constellium reduces its carbon footprint, aligning with sustainability goals and minimizing aluminum production’s environmental impact.
Long-Term Goals and Future Developments in Recycling
This collaboration is part of Constellium’s larger efforts to increase recycled aluminum in its products. The company aims to source 50% of its metal inputs from recycled aluminum by 2030. While the focus is currently on preconsumer scrap, Constellium also investigates ways to recycle postconsumer scrap, such as “twitch”—a mixed aluminum fraction from auto shredders. Although LIBS has shown promise, challenges remain regarding cost-effectiveness and purity. However, as the use of wrought aluminum increases in vehicles, Constellium believes LIBS will become more viable for postconsumer scrap recycling, enhancing aluminum’s circularity.
Overcoming Challenges in Postconsumer Scrap Recovery
Significant progress has been made with preconsumer scrap, but postconsumer scrap recovery still presents challenges. “Twitch” scrap, often derived from auto shredders, contains impurities like zinc, magnesium, and iron, making it difficult to reuse in high-quality applications. LIBS shows promise in recovering wrought aluminum from this fraction, but experts are still evaluating its cost-effectiveness. Constellium remains optimistic that as the amount of wrought aluminum in vehicles increases, LIBS will make postconsumer scrap recycling more efficient in the future.
Leave a Reply
You must be logged in to post a comment.