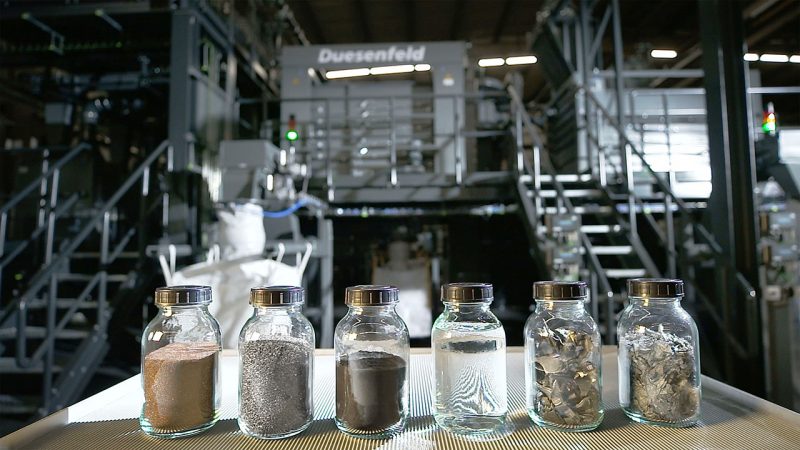
German recycling technology innovator, Duesenfeld, has developed a cutting-edge system designed to recycle lithium-ion battery scrap. The company claims its technology not only recovers marketable metals but also graphite and electrolytes, creating a more sustainable approach to battery recycling. With a focus on maximizing material recovery and minimizing energy consumption, Duesenfeld is setting new standards in the recycling of battery materials.
Revolutionary Three-Stage Recycling Process
Duesenfeld’s recycling system combines mechanical, thermodynamic, and hydrometallurgical processes, starting with the discharging of end-of-life lithium-ion batteries. In its mechanical recycling stage, the company has achieved a 72% recovery rate of materials. This stage reduces the battery to its components without producing harmful pollutants.
The company then uses its hydrometallurgical process to further refine the materials, increasing the overall recycling rate to 91%. This process produces Duesenfeld Black, a material containing electrode active materials and conductive salts. The only components not currently recovered are the separator film and the high-boiler portion of the electrolyte.
High Recovery Rates and Low Environmental Impact
Duesenfeld engineers its process to operate at low temperatures, which prevents the production of toxic hydrogen fluorides, a common byproduct in conventional battery recycling. Additionally, the firm eliminates the need for exhaust gas scrubbing during the mechanical processing stage, which reduces environmental impact.
The process also removes fluorides efficiently during the hydrometallurgical stage, ensuring that harmful substances are handled safely. Duesenfeld focuses on producing high-quality secondary raw materials suitable for use in new batteries, rather than using them for other purposes like paving materials.
Efficient Use of Resources and Improved Battery Performance
One of Duesenfeld’s key advancements is its patented “deep discharge” technique, which recovers energy embedded in end-of-life batteries. The company’s mechanical recycling process is highly demanding, primarily due to the flammability of lithium-ion batteries. The process involves comminuting the batteries under an inert gas atmosphere and using vacuum distillation to recover the electrolyte solvent. This recovered solvent is then sent to chemical industry customers for further processing.
Shredded dry electrode scrap from battery cell production is sorted by physical properties such as size, density, and magnetic and electrical characteristics. This material is then processed to recover valuable metals, including iron, copper, and aluminum, which are sold to established markets.
Pilot Project Success and Industry Implications
In a recent pilot project, Duesenfeld achieved a recycling rate exceeding 90% for industrial nickel manganese cobalt (NMC) cathode scrap. The process also produced a remarkably low fraction of aluminum impurities. Laboratory testing further demonstrated that cells with 26% recycled content performed similarly to those made from primary materials, showcasing the effectiveness of Duesenfeld’s technology.
Conclusion: Paving the Way for Sustainable Battery Recycling
Duesenfeld’s innovative system represents a major step forward in the recycling of lithium-ion batteries. The company’s technology maximizes material recovery while minimizing environmental impact, setting a new benchmark in the industry. By providing a solution that recovers valuable metals, graphite, and electrolytes, Duesenfeld is helping to build a more sustainable future for battery production and recycling.
Leave a Reply
You must be logged in to post a comment.