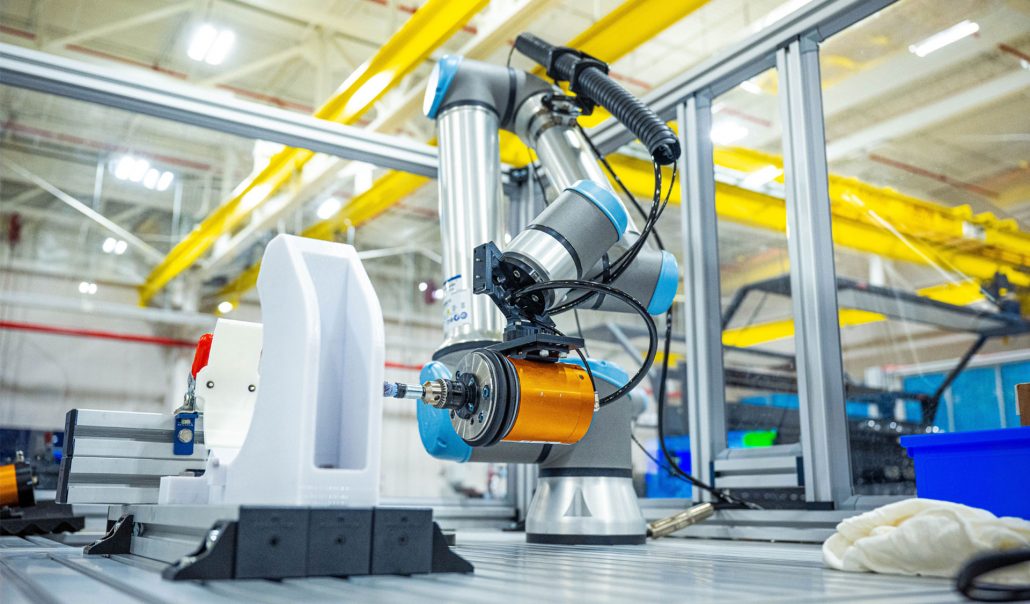
Lockheed Martin has expanded its additive manufacturing (AM) capabilities by adding 16,000 square feet of space at its Grand Prairie, Texas facility. This move is part of the company’s broader strategy to integrate 3D printing into its production processes, positioning AM technology as a core component in both current and future product designs. This expansion underlines Lockheed Martin’s commitment to staying at the forefront of manufacturing innovation, with AM enabling faster, more flexible production methods for a range of critical aerospace and defense applications.
New Technologies and Enhanced Manufacturing Capabilities
The expanded facility now houses large-format, multi-laser metal 3D printers from Nikon SLM Solutions, offering Lockheed Martin the ability to create high-precision, complex metal parts. These printers, along with the addition of heat treatment and inspection equipment, bolster the company’s capability to rapidly produce parts for both high-volume and low-volume production runs. The integration of these advanced systems aligns with Lockheed Martin’s goal of offering modular, cost-effective designs and streamlining the production process for its defense and aerospace customers.
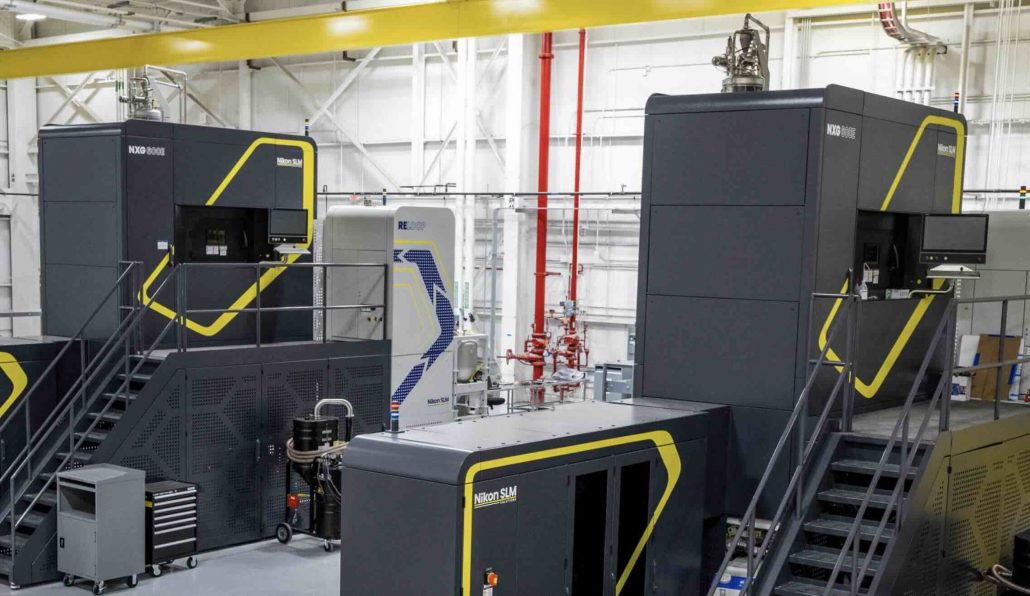
AM as a Strategic Tool for Design and Supply Chain Risk Reduction
Lockheed Martin’s 1LMX digital transformation program plays a key role in incorporating additive manufacturing early in the design phase to reduce both technical risks and supply chain risks. By using AM to replace traditional components like heat exchangers, brazements, and castings, Lockheed Martin aims to lower the cost and complexity of parts while improving design flexibility. This proactive approach to product development not only speeds up the prototyping and production process but also ensures more resilient and adaptable supply chains for mission-critical components.
Proven Success in High-Precision Defense Applications
Lockheed Martin has already seen substantial benefits from AM in its defense projects. One notable example is the use of 3D printing for the Mako hypersonic missile program, where guidance housings and tail fin parts were produced 10 times faster and at one-tenth the cost compared to traditional methods. This success has been mirrored in other projects, including the production of F-35 simulator cockpits and components for GMLRS precision-strike rockets. The implementation of AM in these projects has led to reduced parts counts, shorter production schedules, and significant cost savings.
Strategic Partnerships and Industry Leadership in Additive Manufacturing
Lockheed Martin has established key partnerships to further its commitment to additive manufacturing. In 2022, the company collaborated with Sintavia, a leading metal AM provider, to enhance its research into metal additive manufacturing as a viable alternative to traditional manufacturing methods. This partnership complements the U.S. government’s AM Forward initiative, which aims to support domestic AM adoption and strengthen supply chains. Lockheed Martin is also investing in innovative technologies, such as Firestorm Labs, a manufacturer of Unmanned Aerial Systems (UAS), which is advancing on-demand UAS production using additive manufacturing cells.
Leave a Reply
You must be logged in to post a comment.