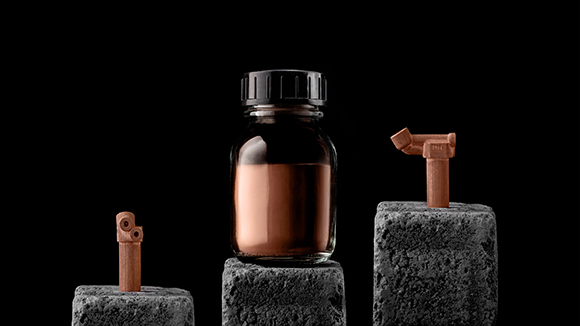
Sandvik Introduces New Metal Powders at Formnext 2024
At Formnext 2024, Sandvik AB will showcase cutting-edge innovations in metal powder solutions. The company will unveil new copper-based alloys and high-performance tool steels for additive manufacturing (AM). These include Sandvik’s Osprey metal powders, like the newly launched copper alloy C18150 and the Osprey HWTS 50 tool steel. These powders are optimized for various 3D printing applications.
Copper and Tool Steel Powders for Additive Manufacturing
Sandvik’s copper-based powders, such as GrCop42 and C18150, offer excellent thermal and electrical conductivity. They are ideal for applications requiring high heat transfer and precise thermal expansion control. These powders come in fine and medium particle sizes. They are perfect for demanding applications like electronics and heat exchangers. Their high CTE (Coefficient of Thermal Expansion) matching is key for components exposed to high thermal stress.
The Osprey HWTS 50 tool steel is a lean hot-work steel with lower carbon content than traditional medium-carbon steels. Despite reduced carbon (~0.22 wt.%), it provides excellent tempering resistance. This improves its performance in additive manufacturing processes, including laser-based AM. The material is also suitable for Hot Isostatic Pressing (HIP) and Metal Injection Molding (MIM). These advancements benefit industries like aerospace, automotive, and tooling, where high strength, toughness, and heat resistance are vital.
Cost-Efficient Titanium Powder for E-Bike Manufacturing
Sandvik’s coarse titanium powder is revolutionizing the additive manufacturing of e-bike components. In partnership with GSD Global, Sandvik developed a cost-effective method for producing titanium parts. This reduces material costs by over 40% and cuts build times by two-thirds. Despite cost reductions, the mechanical properties required for high-performance e-bike frames remain intact. This innovation showcases Sandvik’s ability to offer both cost savings and improved efficiency in manufacturing.
Discover Sandvik’s Innovations at Formnext 2024
Sandvik invites professionals to visit their booth at Formnext 2024, Hall 11, Booth E32. They will have the chance to explore Sandvik’s latest metal powder innovations. Material specialists will be available to discuss how Sandvik’s powders can solve manufacturing challenges. The event offers opportunities to unlock new possibilities in various industries.
Leave a Reply
You must be logged in to post a comment.